www.magazine-industry-usa.com
16
'23
Written on Modified on
AUTODESK-LED COLLABORATION BRINGS AI-POWERED, CLIMATE-FRIENDLY SOLUTION TO AFFORDABLE HOUSING
Known as The Phoenix, the new project will consist of 316 affordable and sustainable homes, built at about half the cost, time, and carbon footprint of a typical multi-family building in the San Francisco Bay Area.
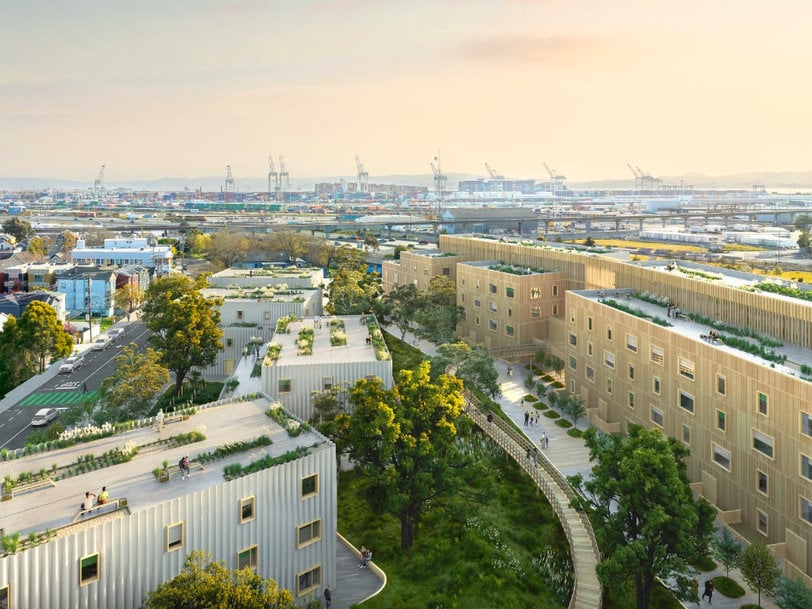
This empty plot of land in West Oakland, California will transform into The Phoenix, a 316-unit affordable and sustainable housing complex.
In 1989, the Phoenix Ironworks Steel Factory in West Oakland, California moved to a smaller location near the marina. The buildings and equipment were dismantled, leaving a 5-acre slab of concrete next to the I-880 freeway. For almost 30 years, the site was empty or underused, even as the population in the region grew, the cost of construction increased, and the housing crisis became more urgent.
Yet within a year, this plot of land will become an innovation village for architects, engineers, and builders who are exploring solutions to housing and climate change. The digital thread connecting these teams and their project data from design to construction is Autodesk’s Design and Make Platform.
The Phoenix will be built at about half the cost, time, and carbon footprint of a typical multi-family building in the San Francisco Bay Area.
To make this possible, the multi-disciplinary team harnessed the power of the Autodesk Platform to share data and workflows and tap into AI-powered insights across the project lifecycle. In the early phases of the project, the team made data-informed trade-offs between goals for operational carbon, embodied carbon, cost, and livability. Later, they leveraged their unit catalogue from past projects to reduce time and risk through reusable design intelligence. And in the final stages, the team is combining physical and digital automation to construct a set of buildings that is both efficient and loved by residents.
AI-assisted design unlocks funding and better livability
The Phoenix is propelled by the California Housing Accelerator. It provides massive incentives for affordable housing projects that can achieve tight timelines impossible with traditional design and construction methods.
Meeting the challenge can unlock billions of dollars in subsidies to build new housing, but it requires creative solutions at every step.
The innovation required to qualify for such funding starts with design. Autodesk and MBH Architects—a successful 34-year-old firm specializing in retail, hospitality, and high-density residential design—have been using The Phoenix to test new technologies and transform traditional workflows.
Using Autodesk Forma for early-stage design, MBH Architects can rapidly explore a huge range of options that meet complex project goals. Adding a floor to a building, nudging the structure’s position north or south, shifting a playground or greenspace from the edge of the development to the center–each move alters the score for cost, carbon, and livability.
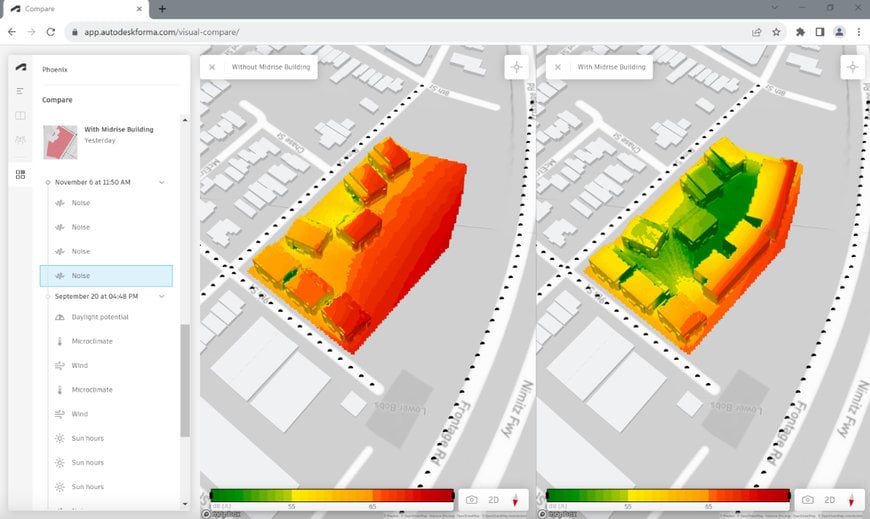
The real-time analysis capabilities of Forma showed the impact of different configurations on livability features like noise from highway traffic.
Industrialized construction powers more predictable building processes
In addition to accelerating and improving design, there is great opportunity in transforming construction. The global population is expected to grow by two billion people in the next 30 years. To create enough housing, workplaces, and schools for this urbanized population, the equivalent of New York City’s worth of buildings must be constructed every month until 2050. And this must be done at the same time as eliminating net carbon emissions from the built environment.
Current construction processes are far too slow and carbon-intensive to meet the challenge. Construction needs to be reinvented, and one way to do this is through manufacturing buildings in a factory. This allows buildings to be more like products than one-offs, and it reduces waste, time, and cost while enhancing safety and reliability. This application of manufacturing principles to the built environment is known as industrialized construction.
The builders of The Phoenix, Factory_OS, have cracked the code for industrialized construction. They use rapid factory production to build housing modules that can be trucked to project locations and assembled by crane. To quickly move models from design to production to residents moving in, the team harnesses Autodesk’s cloud-based workflows for collaboration.
With a focus on prefabrication, this innovative process removes the unpredictability of a traditional construction site. And the convergence of design, construction, and manufacturing workflows dramatically accelerates the speed to completion. The Phoenix units will be erected in about two weeks whereas traditional processes typically take close to a year.
New materials enable buildings to become carbon-negative
One challenge in creating sustainable affordable housing is the building facade. The facade often accounts for more than 20% of a building’s embodied carbon, and finding low-carbon materials can be difficult due to demanding performance requirements like durability and fire resistance. At the same time, the facade is often time-consuming to construct. While Factory_OS’s housing modules can be stacked onsite in about ten days, the facade often takes six months to install. This is due to the need for scaffolding and different subcontractors to install separate layers.
MBH Architects, Factory_OS, bio-materials company Ecovative, building envelope consultant Heintges, and Kreysler & Associates, a pioneer in using advanced composites for facades. Together, the team created a revolutionary 38-foot-long prefabricated facade panel that drastically reduced construction time and embodied carbon.
The panel starts at Ecovative, which grows sustainable biomaterials by combining agricultural byproducts such as corn stover with the living rootlike structure of mushrooms called mycelium. Custom-engineered mycelium parts from Ecovative became the core inside a fiber-reinforced-polymer (FRP) shell produced by Kreysler & Associates.
The mycelium core offers carbon sequestration, and the FRP shell provides durability. The result is a first-of-its-kind facade system with very large panels that are carbon-negative—the process of making them involves more carbon absorbed than emitted, due to the large volume of plant-based material that drew carbon out of the air as it grew.
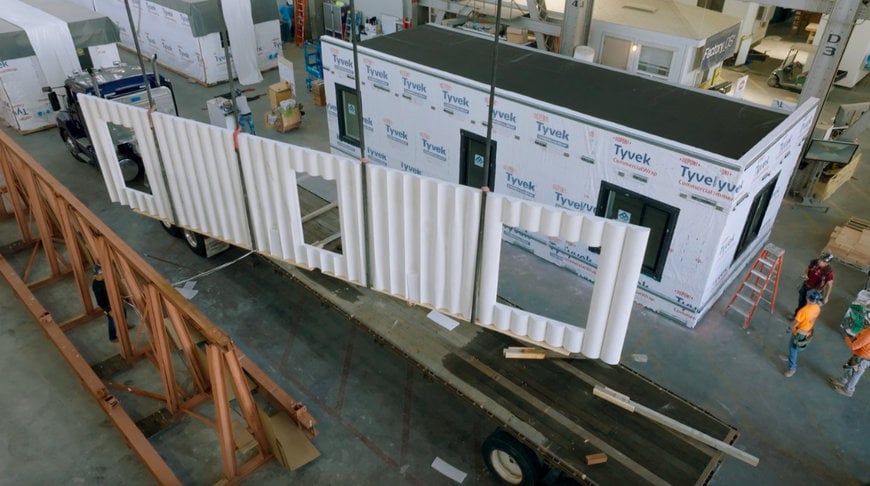
This first-of-its-kind prefabricated facade panel drastically reduces construction time and embodied carbon for The Phoenix.
These novel panels provide five layers of facade performance—structure, waterproofing, fire resistance, thermal insulation, and acoustic dampening—and they can be used as-is with today’s building codes and construction methods.
Scalable processes drive the buildings of the future
This is just the beginning. All the explorations and inventions from The Phoenix are generalizable to future projects. Factory_OS plans to use the new data exchange workflows on future affordable housing projects. MBH Architects is applying Forma and the outcome-based design techniques from The Phoenix to projects beyond housing, such as life sciences buildings. Ecovative and Kreysler & Associates see this project as the first important step towards commercial development of a carbon-negative building facade system.
In 1989, the Phoenix Ironworks Steel Factory in West Oakland, California moved to a smaller location near the marina. The buildings and equipment were dismantled, leaving a 5-acre slab of concrete next to the I-880 freeway. For almost 30 years, the site was empty or underused, even as the population in the region grew, the cost of construction increased, and the housing crisis became more urgent.
Yet within a year, this plot of land will become an innovation village for architects, engineers, and builders who are exploring solutions to housing and climate change. The digital thread connecting these teams and their project data from design to construction is Autodesk’s Design and Make Platform.
The Phoenix will be built at about half the cost, time, and carbon footprint of a typical multi-family building in the San Francisco Bay Area.
To make this possible, the multi-disciplinary team harnessed the power of the Autodesk Platform to share data and workflows and tap into AI-powered insights across the project lifecycle. In the early phases of the project, the team made data-informed trade-offs between goals for operational carbon, embodied carbon, cost, and livability. Later, they leveraged their unit catalogue from past projects to reduce time and risk through reusable design intelligence. And in the final stages, the team is combining physical and digital automation to construct a set of buildings that is both efficient and loved by residents.
AI-assisted design unlocks funding and better livability
The Phoenix is propelled by the California Housing Accelerator. It provides massive incentives for affordable housing projects that can achieve tight timelines impossible with traditional design and construction methods.
Meeting the challenge can unlock billions of dollars in subsidies to build new housing, but it requires creative solutions at every step.
The innovation required to qualify for such funding starts with design. Autodesk and MBH Architects—a successful 34-year-old firm specializing in retail, hospitality, and high-density residential design—have been using The Phoenix to test new technologies and transform traditional workflows.
Using Autodesk Forma for early-stage design, MBH Architects can rapidly explore a huge range of options that meet complex project goals. Adding a floor to a building, nudging the structure’s position north or south, shifting a playground or greenspace from the edge of the development to the center–each move alters the score for cost, carbon, and livability.
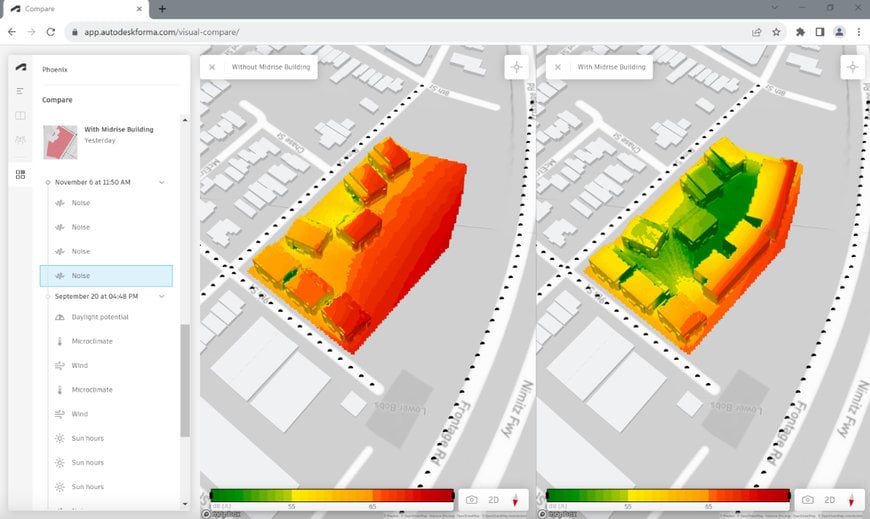
The real-time analysis capabilities of Forma showed the impact of different configurations on livability features like noise from highway traffic.
Industrialized construction powers more predictable building processes
In addition to accelerating and improving design, there is great opportunity in transforming construction. The global population is expected to grow by two billion people in the next 30 years. To create enough housing, workplaces, and schools for this urbanized population, the equivalent of New York City’s worth of buildings must be constructed every month until 2050. And this must be done at the same time as eliminating net carbon emissions from the built environment.
Current construction processes are far too slow and carbon-intensive to meet the challenge. Construction needs to be reinvented, and one way to do this is through manufacturing buildings in a factory. This allows buildings to be more like products than one-offs, and it reduces waste, time, and cost while enhancing safety and reliability. This application of manufacturing principles to the built environment is known as industrialized construction.
The builders of The Phoenix, Factory_OS, have cracked the code for industrialized construction. They use rapid factory production to build housing modules that can be trucked to project locations and assembled by crane. To quickly move models from design to production to residents moving in, the team harnesses Autodesk’s cloud-based workflows for collaboration.
With a focus on prefabrication, this innovative process removes the unpredictability of a traditional construction site. And the convergence of design, construction, and manufacturing workflows dramatically accelerates the speed to completion. The Phoenix units will be erected in about two weeks whereas traditional processes typically take close to a year.
New materials enable buildings to become carbon-negative
One challenge in creating sustainable affordable housing is the building facade. The facade often accounts for more than 20% of a building’s embodied carbon, and finding low-carbon materials can be difficult due to demanding performance requirements like durability and fire resistance. At the same time, the facade is often time-consuming to construct. While Factory_OS’s housing modules can be stacked onsite in about ten days, the facade often takes six months to install. This is due to the need for scaffolding and different subcontractors to install separate layers.
MBH Architects, Factory_OS, bio-materials company Ecovative, building envelope consultant Heintges, and Kreysler & Associates, a pioneer in using advanced composites for facades. Together, the team created a revolutionary 38-foot-long prefabricated facade panel that drastically reduced construction time and embodied carbon.
The panel starts at Ecovative, which grows sustainable biomaterials by combining agricultural byproducts such as corn stover with the living rootlike structure of mushrooms called mycelium. Custom-engineered mycelium parts from Ecovative became the core inside a fiber-reinforced-polymer (FRP) shell produced by Kreysler & Associates.
The mycelium core offers carbon sequestration, and the FRP shell provides durability. The result is a first-of-its-kind facade system with very large panels that are carbon-negative—the process of making them involves more carbon absorbed than emitted, due to the large volume of plant-based material that drew carbon out of the air as it grew.
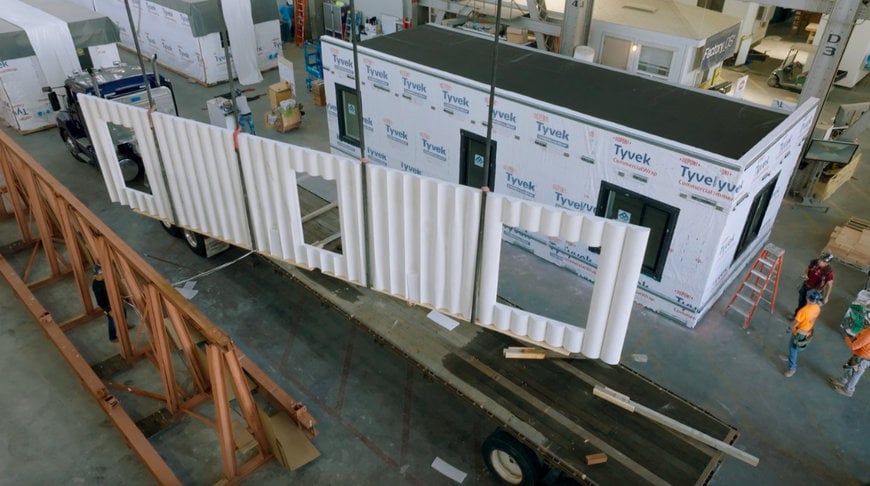
This first-of-its-kind prefabricated facade panel drastically reduces construction time and embodied carbon for The Phoenix.
These novel panels provide five layers of facade performance—structure, waterproofing, fire resistance, thermal insulation, and acoustic dampening—and they can be used as-is with today’s building codes and construction methods.
Scalable processes drive the buildings of the future
This is just the beginning. All the explorations and inventions from The Phoenix are generalizable to future projects. Factory_OS plans to use the new data exchange workflows on future affordable housing projects. MBH Architects is applying Forma and the outcome-based design techniques from The Phoenix to projects beyond housing, such as life sciences buildings. Ecovative and Kreysler & Associates see this project as the first important step towards commercial development of a carbon-negative building facade system.
www.adsknews.autodesk.com