www.magazine-industry-usa.com
03
'15
Written on Modified on
The stiffness of Rack-and-Pinion axis Drive, the key factor for the world class machine-tools builders
To keep total control on their drives systems is one of the most critical points to ensure the performance of the most modern machine tools at their highest level. These drives, either linear or rotary, are the ones which make possible to position the tool and/or the workpieces quickly, accurately, and under control. The mechanisms which compose these systems of drive are generally classified according to their capacities of speed and acceleration, to the power which they are able to transmit, to their precision of movement, to their stiffness, their dimensions, and their reliability.
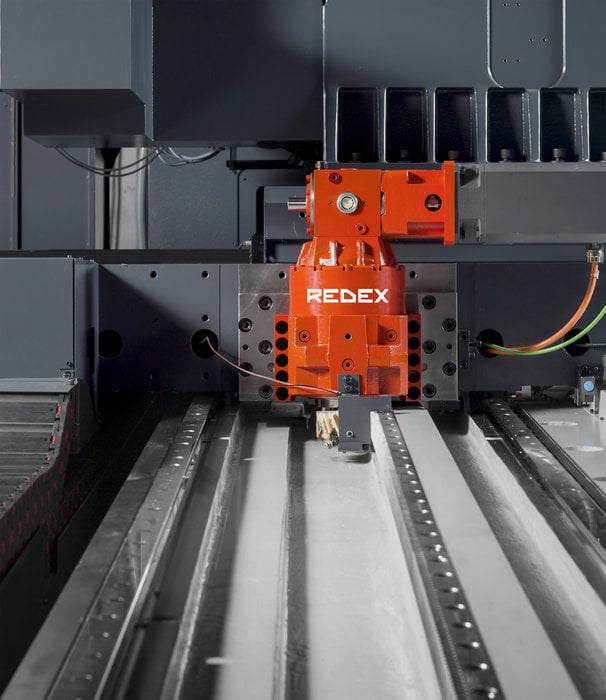
The linear motors are generally used only for the movements of reduced masses. Their limited output and the strong values of their requested current supply them cannot really fit with the high masses. So, the total energy efficiency of this type of solutions can hardly be kept at its optimal level. And the particular precautions which are essential during the setting-up operations is also an important barrier to their use.
If the ball screws are rather well adapted to limited linear movements -as up to 4 meters- their precision and their rigidity can be seriously called into question, as long as this technology being able to induce significant errors cumulated on long courses. And whatever the distance, short and repetitive movements generate heating, local dilation and affect the precision.
On a distance of four meters, one considers that an endless screw can involve an error going until several tenth of millimeters.
On the same distance, a rack-and-pinion drive is usually considered to generate an error of about only few microns.
By design, the rack-and-pinion drive systems are offering, a better moment of inertia (lower), a higher natural frequency, a better efficiency and a total precision independent the length of the displacement. Not to mention that one of their biggest advantages compared to ball screws is their versatility, particularly in terms of flexibility on the installed length. The setting-up is faster and simpler, which lead a better reliability, easier maintenance operations and at the end of the day, a matchless TCO(1) .
Stiffness is the key
In their constant evolution towards higher levels of precision and better dynamic performances, the rack-and-pinion drives ran up nevertheless until now against some specific problems of their own. Taking into account their integration in complex closed loop control systems, the main reservations to generalize their use were most often the backlash issues - between the pinion and the rack, the inaccuracy for precisely reaching the target, and the vibrations (when being too close to the natural frequencies of the driven equipment).
At first, the backlash issues - between the pinion and the rack were solved by the combined use of of mechanical or electric preload applied to reducers installed by pairs. This solution makes it possible to definitely cancel 100% of the backlash between the pinion and the rack.
Meanwhile, REDEX's engineers have been able to dramatically improve the total linear rigidity of the system. Because the higher the stiffness of each part of rack-and-pinion drives, the easier the parameter setting of the control loop. And the more precise is also the transmission of the movement (no more inaccuracy to reach the target, natural frequency pushed back upwards).
Moreover, the improvement of rigidity passes not only by single parts as resistant as possible to the deformation but also by their optimization of their integration, at the same time in a robust and compact way.
The stiffness level of a linear drive is given in relation to the driven axis, on which the composition of the force applies.
The Composite Stiffness (total) thus results from the sum of its three components:
-Torsional stiffness : Depends on the internal planetary gear system. It is the resulting angular deformation to which the system is subjected when the entry of the reducer is blocked and when a torque is applied at the output.
-Radial stiffness : Depends on the flexion of the shaft connecting the reducer to the rack.
-Axial stiffness : Depends on the deformations along this same axis.
One considers that 60% of the overall stiffness comes from the radial component, a field in which Redex solutions are particularly distinguished from those of other solutions on the market. This extreme stiffness is the result of an exclusive design:
-The unique design of the shafted pinion (the teeth are machined directly on the shaft).
-The shortened distance between the point of contact with the rack and the bearings housing
-The choice to use generously oversized bearings and optimized preload procedures
These key points of design are the one with the highest influence on the radial component of stiffness, thus contributing to an incredibly high composite stiffness allowing REDEX drives to defy any competition. In addition to, torsional and radial stiffness features of REDEX are validated at 100% during the tests carried out for each reducer delivered, by making sure that they are always exceeding the rated technical specifications.
But for the manufacturers, rigidity is not the only stake to be taken into account in the TCD(2). The facility of integration and assembly are also fundamental.
“Cubic concept” of REDEX
Along the few past years, the major part of the world class machine tools builders have adopted the “cubic concept”, invented and developed by REDEX to optimize the complete axis drive solutions offered to the manufacturers.
It's true that the “Cubic concept” is offering many assets, to start with significant savings.
This exclusive design allows to forget the need for ultra-precise extensions to the frame of the machine (where the reducers were usually integrated), because the frame which is hosting the axis drives does not form anymore a extension of the machine frame but an extension of the drive itself. It's an great advantage, which simplifies a lot the machine design, saves many hours of stiffness simulation on sophisticated CAD 3D software, not to mention the R&D and natural size test campaigns, and the industrial risks which are attached to such a development. The implementation procedure is also quite simplified with only the request of machining much simpler shapes on the interfaces of fixing sides
.
To make it short, the “Cubic concept” makes possible to offer an incredibly rigid planetary reducer with very weak angular backlash, fully integrated in its own cubic frame and ready to be installed on the main frame of the machine exactly as if would belong to the frame itself.
This exclusive design is applied to the most innovative products of REDEX in the range of its solutions of rack-and-pinion axis drives.
(1) TCO: Total Cost of Ownership
(2) TCD: Cost total of Design
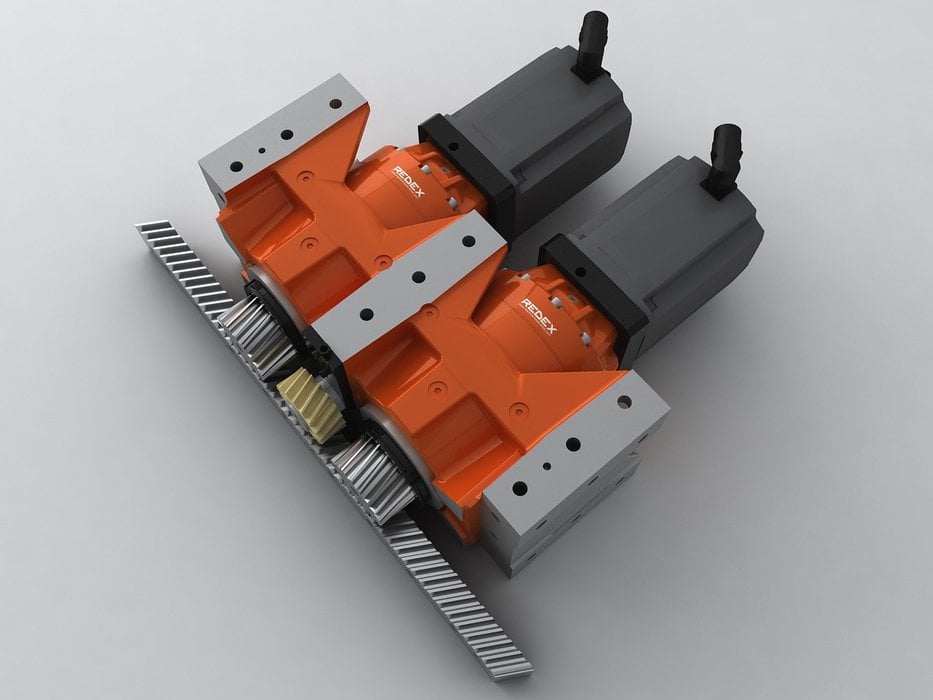
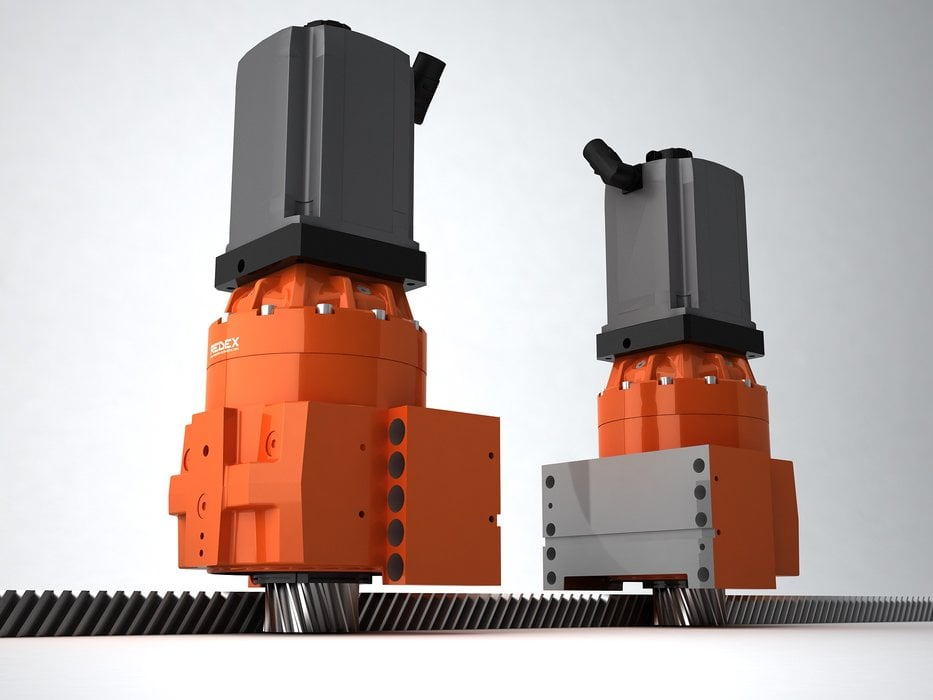
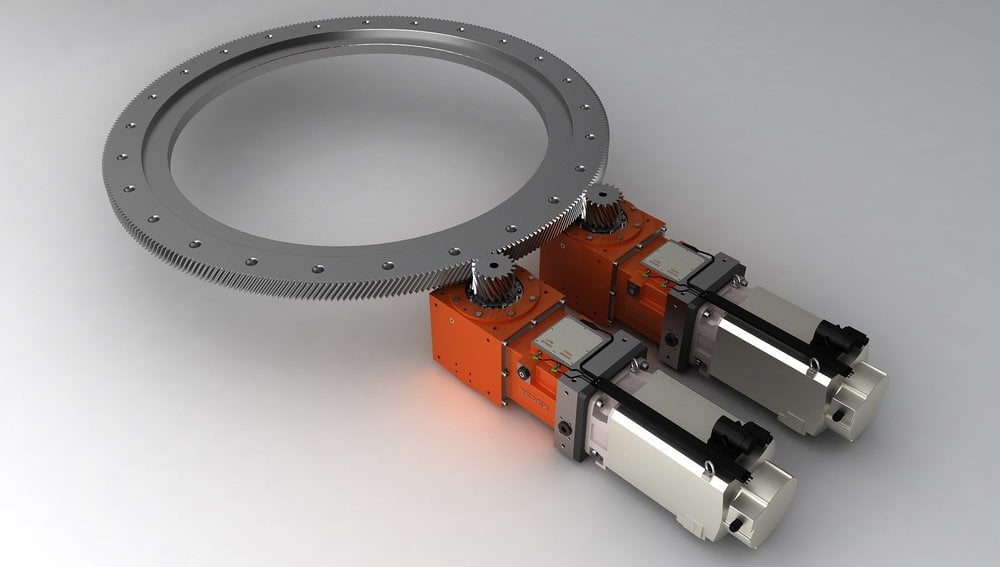