www.magazine-industry-usa.com
04
'21
Written on Modified on
Systems-Level Thinking Key To Lowering Cost Of EVS, Says ESI Automotive
A systems-level approach to electric vehicle (EV) development is essential to calculating potential gains in vehicle efficiency and build costs required to bring the total cost of the EV powertrain down. That’s the message from ESI Automotive at a time when the US is pushing for half of new cars sold in the country to be battery-powered by the end of the decade.
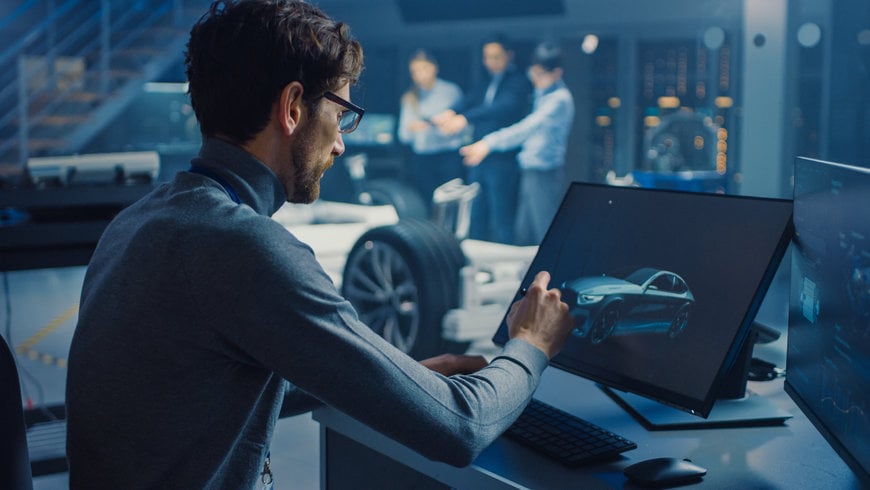
The Biden administration recently stated its intent to invest billions of dollars into charging stations for EVs and introduce point-of-sale rebates for consumers purchasing EVs to alleviate cost pressures. Automakers have backed the move, committing to end internal combustion engine (ICE) vehicle production and kickstart EV manufacturing. However, the country remains in a precarious state: three percent of new cars sold in the United States in the first half of 2021 were electric1 - a far lower rate than China and Europe - which offer more generous incentives and have stricter auto-regulations.
A major barrier to EV adoption in the States is the cost of EVs. At the high end of the EV market, a Tesla Model S starts at more than $80,000, and at the low end, a Chevrolet Bolt starts at $31,000 — nearly $10,000 more than a larger gasoline-powered sedan like the Chevy Malibu. Reaching price parity with ICE cars is key to ensuring greater adoption of EVs.
Chris Klok, director of vehicle electrification at ESI Automotive believes that it is possible for OEMs to make both cost savings and vehicle efficiency improvements by viewing the entire design and production process at a systems-level.
“By viewing vehicle manufacturing at a systems-level, it is possible to understand where significant savings can be made, which can contribute to lowering the overall resale price of EVs, making them more competitive.
“For example, silver sintering technology delivers proven benefits to the inverter in terms of increasing overall vehicle range and performance by boosting thermal and electrical conductivity. As part of the powertrain system, sintering contributes to a decrease in bottom line expenditure.
“Furthermore, sintering has been proven to improve power-density to the inverter, increasing range and eliminating the need – and cost – of additional battery content.”
According to Klok, key to automakers being able to identify these efficiency and cost improvements is a more collaborative approach to working with the vehicle supply chain. The formation of technology partnerships can enable OEMs to improve powertrain efficiencies with the assistance, experience and support of more established technology partners.
1Electric vehicle sales surge in 2021 (power-technology.com)