www.magazine-industry-usa.com
16
'21
Written on Modified on
Robotic Assembly of Sensors in an Industry 4.0 Environment
Flexibility in Its Purest Form.
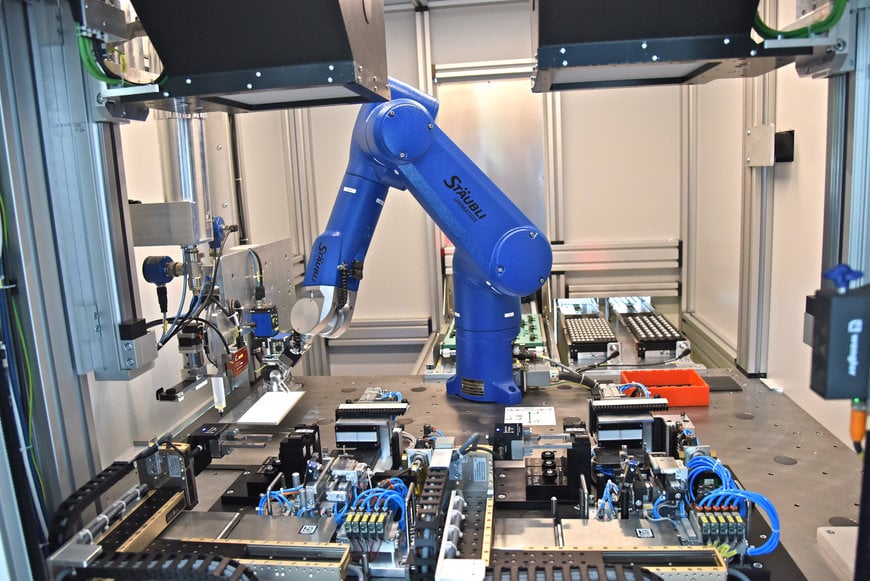
Sensor manufacturers have to be innovative, because the accuracy and reliability of their products is crucial in digitally integrated processes. One such manufacturer is wenglor. The intelligently designed assembly cell installed in the company’s factory at Tettnang on Lake Constance is testimony not only to the pioneering nature of its products but also the methods by which they are produced.
The walk from the parking lot to the main building is enough to convince visitors that wenglor has prospered in recent years. The number of new buildings on its Tettnang campus is an indication of the considerable investment that has gone into the company. And as Michael Martin, a software developer at wenglor assures us, the upward trend shows no sign of abating “Our business continues to boom,” he says. “We are already planning the next phase of construction to meet the huge demand for smart sensor technologies. We are benefiting greatly from the growth of Industry 4.0, which is driving the sensor market.”
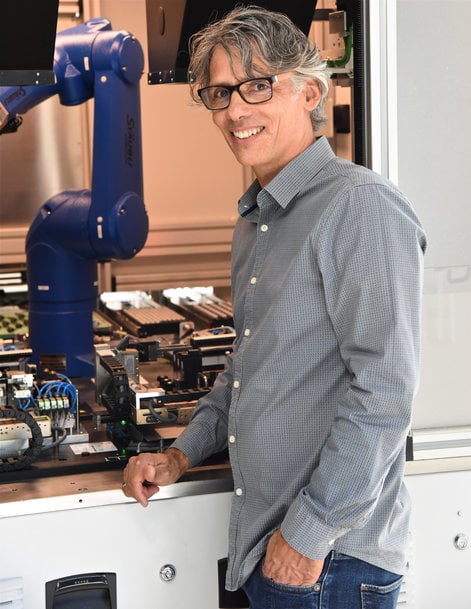
Michael Martin, software developer at wenglor, is pleased about the positive direction in which the sensor market is moving.
Wenglor employs no fewer than 300 people at its Tettnang site alone and is barely able to meet the need for qualified personnel. In such circumstances, efficient, highly automated production concepts offering maximum performance in terms of output and quality are a top priority. A robot cell in which optics modules for different optoelectronic sensor series are assembled quickly and precisely shows what such solutions look like in practice. Key cell components include a Stäubli TX60L six-axis robot, a Beckhoff TwinCAT3 soft PLC, and a .NET host program.
Martin describes the special nature of the cell: “The robot program supports any specifications, the execution steps in the PLC are freely configurable, and the tooling of the cell is highly flexible which gives us a lot of freedom. The system therefore not only adjusts lenses but also masters a wide range of assembly applications.”
At present, only optics modules for various modular sensor series are assembled in the cell but the possibilities verge on infinity. Typical batch sizes range from 100 to 2,000 optics modules and the cell may need to be retooled up to five times per day. But the entire cell can be retooled in just a few minutes due to the flexibility of the system and the control technology of the host program, from which the applicable process sequences need only be called up.
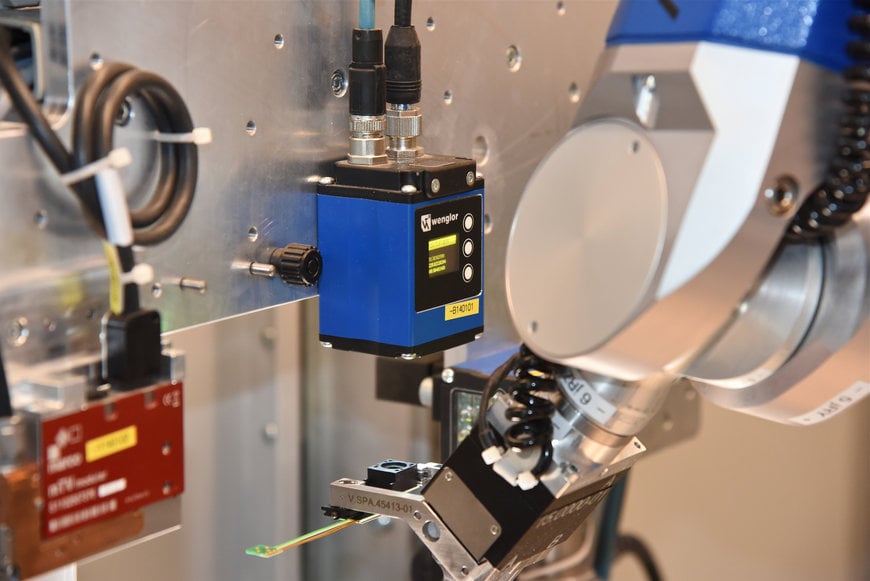
The smart camera detects the exact position of the optics module in the gripper so that it can later be placed in the mounting position with the requisite level of accuracy.
The Assembly Process at a Glance
The Stäubli TX60L six-axis model performs most of the handling processes for the three optics module components, transmitting lens and receiving lens, which come and go on trays. The L in the model name stands for “long-arm version”, in this case a range of 920 mm, which is more than enough to reach all stations within the cell.
The process begins with the robot picking up a lens-less optics module. The TX60L is equipped with a gripper that is configured and controlled via IO-Link. Because the arrangement of the modules in the tray is not exactly defined, the robot first moves to a station where the position of the componenta is captured by the wenglor weQube smart camera. Only then can the module be positioned with the requisite accuracy ready for assembly.
Next, the robot arm steers across to a station where adhesive is applied to the module’s lens seats. Now, the TX60L only needs to place the component precisely in its holder and part one of the handling process is complete. At its assembly position, the optics module is clamped, connected and configured via IO-Link.
“Positioning the module in its holder requires high precision from the robot,” adds Martin. “We are working within tolerances of a few hundredths of a millimeter. The Stäubli robot easily complies with these accuracy requirements and handles positioning with speed and accuracy.”
Precision Work: Adjustment of the Lenses
Subsequently, the robot sets about handling the transmitting lens and the receiving lens. The work steps are identical: The TX60L picks up one lens at a time and carries it across to the smart camera survey station, which determines the lens’s position in the gripper and places it in a transfer position.
At this station, a high-precision linear system handles and adjusts the lenses in the optics module. Despite the exemplary precision of the Stäubli robot, this task could not be managed with the six-axis model. As Martin explains “The transmitting and receiving lenses must be precisely adjusted within a few micrometers, which is only possible with an ultra-precise linear system. This adjustment is the most important step in the assembly process.”
Positioning of the lenses relies on an optical feedback system consisting of the wenglor smart camera, the PLC, the linear system and a 3D control algorithm. If the size and position of the light spot are found to be within the specified window of tolerance, the adjustment algorithm stops and the adhesive is allowed to cure. In the last step, the Stäubli robot takes the optics module and places it in its tray.
This innovative production technology ensures that all wenglor sensors in the optoelectronic PNG//smart series have identical optical properties, which greatly benefits wenglor’s customers around the world.
To shorten cycle times, the adjustment station is duplicated. Thanks to its high dynamics, the Stäubli robot can operate both identical stations alternately. All communication between the separate elements of the cell is via EtherCAT. Therefore the EtherCAT option was a deciding factor in selecting the robot.
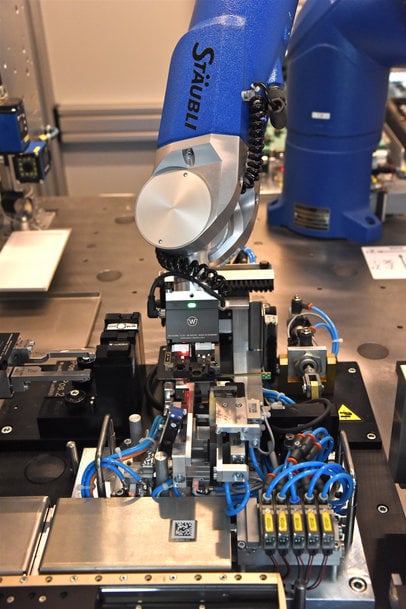
The TX60L manages most of the handling processes involving the three individual parts – optics module, transmitting lens and receiving lens – which come and go on trays.
Digitization for Unprecedented Flexibility
While many people still speak of Industry 4.0 in the abstract, wenglor’s team of development engineers have already implemented the relevant standards in this cell “We put together the processes to be carried out as a sequence of ‘atomic’ steps which we can configure as required,” says Martin. “The number of individual steps can vary greatly, ranging from 1,000 in the lens adjustment to 30,000 in the more complex tasks. For each step, all relevant parameters are stored, so that the process flow can be traced to the smallest detail.”
With its groundbreaking assembly cell, wenglor shows how modern control technology and high-performance robots can take both productivity and flexibility to new levels. The system meets all expectations and does its job with maximum availability, if it is no longer tasked with lens adjustment one day, it could be assembling connectors the next. A more future-proof investment is hard to imagine.
www.staubli.com