www.magazine-industry-usa.com
07
'21
Written on Modified on
CHICAGO HEIGHTS STEEL UPGRADES CONTROL SYSTEM, REDUCES DOWNTIME
Partnering with the right team makes updating a complete control and electrical system simple for the rail re-rolling customer.
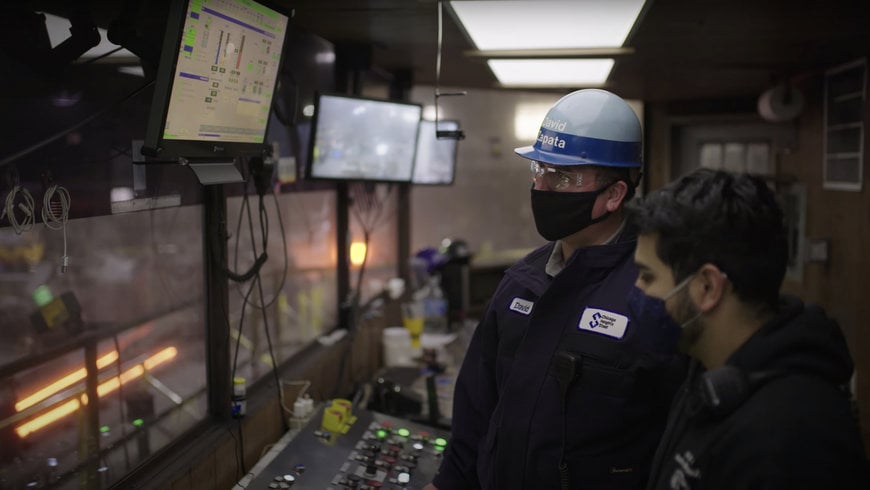
Background information
Running a steel mill on an obsolete control and electrical system not only impacts productivity, but it can also pose safety risks. And without replacement equipment readily available or a team of technical specialists at the ready to fix outdated machines, mills are facing a real risk of long-term downtime and loss of production when a system goes down.
While updating a complete control and electrical system seems like a great undertaking, partnering with the right team can make the process quite smooth. Chicago Heights Steel shares their story.
About the customer
Chicago Heights Steel is a rail re-roller that has been in business since 1893 and operates out of Chicago, Illinois in the United States. The company buys old railroad rail, heats it up, and splits it into three sections. From those pieces, they run different products: signposts, T posts and some specialty products.
The challenge
An obsolete control and electrical system was causing downtime and preventing Chicago Heights Steel from producing at capacity.
“Every time they were having an electrical problem, they were spending a lot of time finding out why things were happening. And even more time to get things solved,” says Antonio Ambra, Business Development Manager at AIC.
“No one alive could fix some of that stuff. There were no parts available. No one knew anything about it,” says Bradley Corral, President of Chicago Heights Steel. The mindset at Chicago Heights Steel is to do whatever it takes to get a job done, so it was important to find a partner who operated the same way.
The solution
Chicago Heights Steel enlisted help from AIC, a Rockwell Automation System Integrator Partner.
Automazioni Industraili Capitanio (AIC) is a global system integrator based in Italy that provides tailored automation and robotic solutions for the steel industry. They have more than 1,000 applications worldwide and over 40 years of experience helping steel customers.
AIC came up with a plan for revamping the entire rolling mill, starting with the head rougher stands where the steel is reduced in size, and going through the takeout of the bar on the cooling beds in the finishing area. The system included:
- New main and auxiliary drives
- Automation & control desks
- HMI control system based on Stratus Server and ThinManager® Thin Client Management Software
- Safety system
- Sensors
- Engineering
- Spare parts
- Remote support services
- Packing and shipping
“The new system has the ability to bring every single PC onto the network, so we can see in real-time what’s going on in the mill,” says Antonio. “And it’s scalable: the system has potentially no limits for future expansion.”
Results
David Zapata, General Supervisor of Engineering and Maintenance at Chicago Heights Steel reports that the new system is reliable, and troubleshooting a problem is much easier now.
“Some of the setup process has shifted from the electrical department to the mill operators because of the simplicity of use and information available. We no longer need electricians to make adjustments or speed changes. This reduces the time it takes to start production and make changes,” he says.
“With the new system, there’s less time I have people standing around waiting for equipment to be back up and running. This increases our lead times for delivery for customers,” says David.
Chicago Heights Steel was so happy with the results that they have signed on with AIC to perform another upgrade project next year, which includes drives, automation and HMI for material handling in the reheating furnace area. This new system will be fully integrated with the mill control system.
“Everything’s going to be Rockwell Automation products again: we always prefer to work with Rockwell Automation,” says Antonio.
“My favorite part of my job is trying to solve customer problems. Every plant has something unique or is facing some problem. I like to look for how to solve things,” says Antonio.
www.rockwellautomation.com
Results
David Zapata, General Supervisor of Engineering and Maintenance at Chicago Heights Steel reports that the new system is reliable, and troubleshooting a problem is much easier now.
“Some of the setup process has shifted from the electrical department to the mill operators because of the simplicity of use and information available. We no longer need electricians to make adjustments or speed changes. This reduces the time it takes to start production and make changes,” he says.
“With the new system, there’s less time I have people standing around waiting for equipment to be back up and running. This increases our lead times for delivery for customers,” says David.
Chicago Heights Steel was so happy with the results that they have signed on with AIC to perform another upgrade project next year, which includes drives, automation and HMI for material handling in the reheating furnace area. This new system will be fully integrated with the mill control system.
“Everything’s going to be Rockwell Automation products again: we always prefer to work with Rockwell Automation,” says Antonio.
“My favorite part of my job is trying to solve customer problems. Every plant has something unique or is facing some problem. I like to look for how to solve things,” says Antonio.
www.rockwellautomation.com