www.magazine-industry-usa.com
29
'21
Written on Modified on
Latest Generation of Prestretch Film Carriages Maximizes Stretch Wrapping Efficiency
Prestretch film carriages have contributed to making automated stretch wrapping of pallets more effective and cost efficient by better managing film usage.
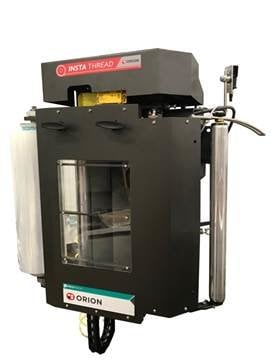
Now, a new generation of automated prestretch carriages has taken film management to the next level – such as the S-Carriage InstaThread® Prestretch Film Carriage recently released from Orion Packaging Systems – providing 180-degree roller contact to
minimize slippage and neckdown, while delivering up to 300 percent prestretch.
The tightening of stretch film around a pallet load is the fundamental mechanic achieved from stretch wrapping, whether applied manually or automated. When the film is stretched around a load, the memory of the film wants to return it to its initial form. The film tightens due to this elastic memory as it tries to return. It is this film memory that differentiates stretch film applications from other means of securing unit loads.
Settling of pallet contents that occurs during warehousing and shipment can loosen film applied with more manual methods of unitizing, whereas film memory if sufficiently stretched, takes up the slack and continues to secure the load. The benefits derived from maintaining pallet-load integrity throughout warehousing and distribution, in terms of reduced product damage, uninterrupted throughput of the pallet contents, and safety, are self-evident.
Manual stretch wrapping of unit loads can achieve 5 to 10 percent of film stretch. Conversely, automated prestretching of film permits it to be stretched to a considerably greater degree. Stretch film has evolved to permit up to 300 percent prestretch depending on the stretch wrapping equipment being used, with the potential of reaching up to 600 percent prestretch currently being tested. But stretch film memory is influenced by the yield point, the amount of stress a material can withstand without permanently having plastic deformation. Prior to reaching the yield point the film will elastically deform but will return to its original shape once the stress is removed.
A representative example of these latest-generation machines is the S-Carriage InstaThread® Prestretch Film Carriage recently released from Orion Packaging Systems. With the latest 180-degree S-pattern roller design – equipped to provide a standard 260 percent prestretch that adjusts up to 300 percent prestretch – the system is engineered to deliver extremely limited slippage between rollers, less neckdown and better film yield. Ultimately resulting in faster wrapping and less film cost per load, the carriage wraps 154 pallet loads per 20-inch film roll, compared to 135 pallets with W-pattern and U-pattern carriages. At this rate, for many manufacturers, film cost saving can exceed $1,200 annually.
S-pattern prestretch carriages typically require the operator to weave the film into the rollers to set-up the machine for proper 180-degree contact. It is always a potential safety risk when fingers are inserted into automated machinery components. This new S-Carriage design bypasses this risk by eliminating the need to thread the film through the rollers. The operator simply pulls the film through and closes the film carriage door, without touching the rollers, making film changeover safer and quicker.
This new generation of film prestretch carriages is equipped with digital and cloud-based connectivity via HMI touchscreen. Each wrap can be set-up with programmed passcode-protected recipes to ensure consistent film is being applied per pre-set parameters. The HMI is recording multiple data sets on each wrap cycle, which can be available in real-time via the cloud for review by plant management.
Automated Prestretch
Today, stretch films are designed to achieve optimal prestretching values that can be attained with high-performance stretch wrap machines. In automated prestretch, the film threads past two rollers – the second roller's rotational speed is faster than the first, thus stretching the film between the two. But how these rollers are positioned and contact the film have a direct impact on the quality of the stretch being applied to the load.
The more contact the rollers have with the film will increase their grip and hold on the film. Most W-pattern and U-pattern design of prestretch carriages will deliver about 90 degrees of contact with the film. Whereas an S-pattern design will exert approximately 180 degrees of film contact.
The S pattern design routes the film around the front of the first prestretch roller, then around the back of the second prestretch roller, dramatically reducing the distance between rollers where the film is actually stretched. More film contact means more control over the film being stretched, resulting in a more uniform stretch being applied to the load.
180-degree film contact gives more consistent and accurate prestretch, which means less slip due to increased surface contact. The distance between the prestretch rollers affects neckdown. Neckdown reduces the width of the film being applied, and therefore, reduces the coverage a revolution of stretch film provides, increasing the number of revolutions required to wrap a pallet.
A standard 20" roll of stretch film being applied through a W-pattern and U-pattern prestretch carriage will lose 15 percent of its width (3 inches) when applied to a pallet due to film neckdown. An S-pattern design with 180-degree, directly adjacent prestretch rollers will reduce film neckdown to 10 percent (2 inches), a one-third reduction in neckdown and a 5 percent increase in film width coverage per stretch.
Latest Generation of Automated Prestretch Carriages – 180-Degree Film Contact, with Up to 300 Percent Prestretch
The latest generation of automated prestretch carriages with 180-degree S-pattern roller design is capable of providing up to 300 percent prestretch with minimized neckdown,. This exceeds the conventional 200 percent prestretch found in most carriages.
Supporting End-of-Line Productivity
The latest technology in prestretch film carriages has contributed to making automated stretch wrapping of pallet loads more effective and cost efficient by better managing film usage.
These new-generation systems have evolved prestretch technology to a level of exceptionally high precision through years of practical end-of-line applications in numerous industries. They incorporate the necessary automation that enable companies to achieve more productivity, increased versatility in application, decreased product damage and realize a more profitable bottom line.
Another factor influenced by stretching is the film's tensile strength, a measurement of the maximum amount of force a material can take without breaking. The greater the tensile stretch measurement, the stronger the film. As the film is stretched below the breaking point, the tensile strength increases, which will reduce shipping damages and increase load stabilization. It is important for a stretch film to have adequate tensile strength for the load it is securing.
Automated prestretching of film has direct implications for maintaining predetermined and consistent stretch wrapping parameters for pallet integrity, while greatly increasing the number of pallets that can be wrapped from a given volume of film when compared to manual pallet wrapping applications. It can increase film strength, improve load integrity, reduce the amount of stretch wrap film needed, and save on stretch film packaging costs.
www.orionpackaging.com