www.magazine-industry-usa.com
08
'21
Written on Modified on
Automotive metal components: Mevis invests in Metrios measuring technology
“Using a manual machine to measure a part with 17 dimensions took about 20 minutes. Today, with the Metrios program, we can do it in just 7 seconds. From 20 minutes to 7 seconds.” "We carry out highly intense inspection, even every half hour. Now our guys on the shop floor are in charge of everything, they are autonomous, they are the masters of their work.".
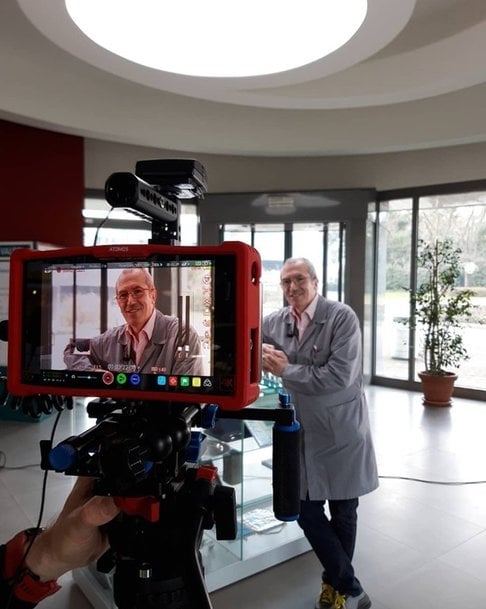
Over 700 employees, 80 million parts per month.
Mevis supplies major multinational market leaders, mainly in the automotive industry, which represents 70% of the company's turnover, followed by the electromechanical, household appliances, and electrotechnical sectors. The company's main products include bent and printed wire parts, welded parts, assembled parts, strip springs, compression springs, and tubular parts.
“To measure sheared and bent parts and CNC production,
we need the right instruments.
These are profile projectors, where you place a part,
and with a specific light you can define the shape and take the measurements.”
we need the right instruments.
These are profile projectors, where you place a part,
and with a specific light you can define the shape and take the measurements.”
8 processing plants.
“MEVIS was founded exactly 60 years ago, we’ll actually be celebrating our anniversary this year.
It all started with the brilliant idea from our founder, Adriano Visentin, to meet the needs that were growing in the spring industry in this local area.
Over the years, he considerably diversified production and today we cover a huge variety of products.”
It all started with the brilliant idea from our founder, Adriano Visentin, to meet the needs that were growing in the spring industry in this local area.
Over the years, he considerably diversified production and today we cover a huge variety of products.”
The group has an extensive and advanced machine park including spring coiling machines, bending machines, torsion spring winding machines, automatic presses, welding plants, and of course, measuring machines. The company invests heavily in latest generation technology to keep a competitive edge in terms of quality, costs, and development times.
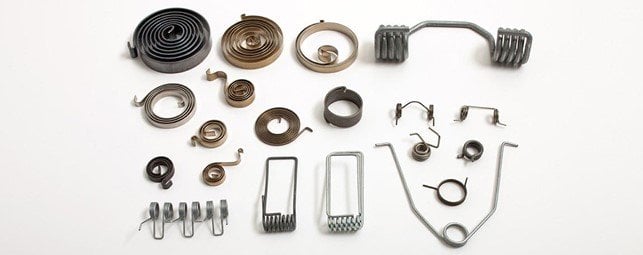
Traditional tools could no longer keep up with demanding production rates.
Quality is a major pillar in the company's business philosophy. It is a necessary aspect of every phase in the production process but requires particular attention in terms of cost containment.
Bruno Sartori, Head of Quality Control, explains how traditional measuring instruments were no longer capable of checking hundreds of parts:
“We used a classic cranked profile projector; we had to turn the dial to see the angles and to align the part. The results were highly subjective and the process was essentially very slow."
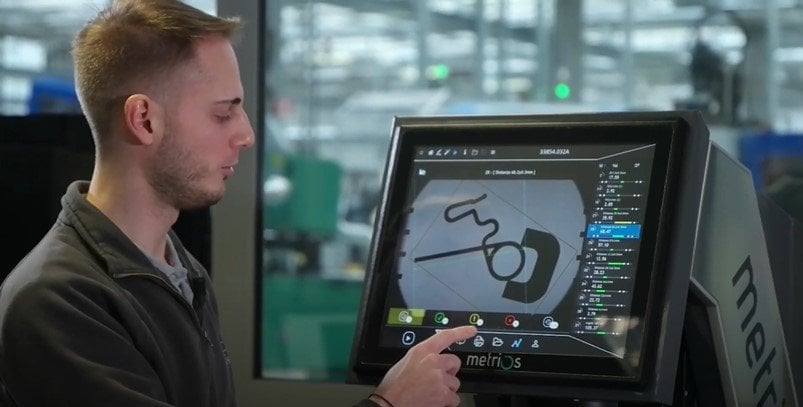
To meet elevated production demands, Mevis operators were carrying out the process controls.
“Our operators had to perform many measurements to guarantee the required level of quality.
This led to a considerable waste of time - up to 20 minutes were lost per code."
This led to a considerable waste of time - up to 20 minutes were lost per code."
The challenge for Bruno Sartori was the following: efficiency had to be improved in this phase, inspection time had to be reduced, and an objective and indisputable result guaranteed. This would have significantly increased both productivity and the quality of parts. We needed a tool that measured parts automatically and even better, several parts at a time.
ASK FREE DEMO
https://go.metrios.net/request_a_demo
The introduction of 4 Metrios measuring machines in Italy and Slovakia.
Today Mevis has three Metrios measuring machines installed in the Italian plant and one in Slovakia. In Italy, one machine was placed in the testing area and the other two on the shop floor.
“These machines measure all the bent and sheared small parts. And that's not all, we manage to measure all the parts that can fit within the field of view, even up to 20 at a time. "
"Take torsion springs, for instance, in just a few seconds we can detect the angles, length of the stems, diameters."
"Take torsion springs, for instance, in just a few seconds we can detect the angles, length of the stems, diameters."
There was an evident increase in productivity after improving the inspection phase.
“What has changed since we introduced Metrios? We have already inserted more than 400 codes.
This means that we have measured over 400 different parts and all the programs that can be pulled up at any time.”
Mevis operators can finally carry out inspections independently and are enthusiastic about using a high-tech tool in production.
“Each operator on the shop floor has an ID badge and calls up the program via barcode. All the measurements taken arrive directly to the server, ready to be processed. Previously everything had to be written by hand!"
“If before, an operator could monitor just 4 plants and take the measurements, today that same person can control the quality of six or seven plants.
Our work supports production because it’s important for the operators to monitor the machine and understand production trends.”
Our work supports production because it’s important for the operators to monitor the machine and understand production trends.”
Sometimes, like we see here, the part might have multiple views.
The good thing about this machine is that with just a few, quick clicks, we can get a pre-set pdf report with all the dimensions analyzed.
“Another important advantage is that, with a manual projector you position one part at a time. But on the Metrios stage, you can measure multiple parts at the same time.”
MEVIS has 4 Metrios machines installed in its plants.The good thing about this machine is that with just a few, quick clicks, we can get a pre-set pdf report with all the dimensions analyzed.
“Another important advantage is that, with a manual projector you position one part at a time. But on the Metrios stage, you can measure multiple parts at the same time.”
ASK FREE DEMO
https://go.metrios.net/request_a_demo