www.magazine-industry-usa.com
05
'13
Written on Modified on
Penetrating through London’s soft clay Rapid Transit tunnel construction in central London
The city of London is currently adding to the East-West rapid transit connection, adding to the current 62 miles public transport network. For this major project, 13 miles of new tunnels are being bored in the city center. The soil consists mainly of soft clay with a consistency that makes the transport of excavated material especially challenging. H+E Logistik and NORD DRIVESYSTEMS, two German industry specialists, are supplying suitable conveying technology including NORD geared motors.
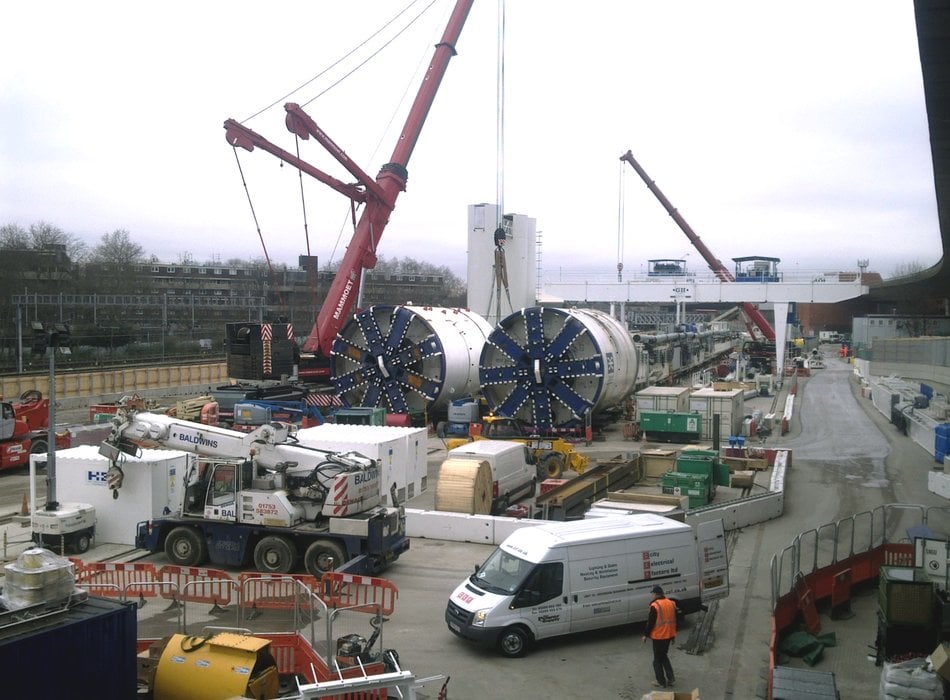
The two tunnel boring machines (TBMs), affectionately called "Phyliss" and "Ada, are named after
mathematician Ada Lovelace and city map pioneer Phyllis Pearsall, and are supplied by German manufacturer Herrenknech. Each "TBN" measures approximately 328ft in length and weighs about 1,000 tons. Phyliss and Ada have been pushing forward their 23ft wide “Cutterhead” blades below the City since 2012. After tackling the distance of 4 miles, between Royal Oak and Farringdon Station, they are planned to resurface in 2015. Besides Ada and Phyllis, more TBMs are currently boring similar tunnels in various other track sections for the East-West connection through London, which will measure a total of 73 miles. The first Crossrail sections will be put into operation in 2018. With an investment volume of more than 23 billion US$, the “London Crossrail” is currently Europe’s largest infrastructure project.
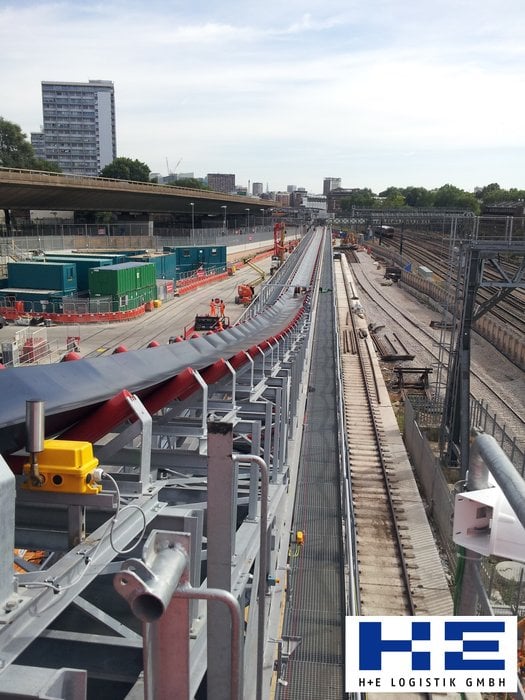
Illustration 2: The project uses German conveying technology: every hour, several thousand tons of excavated material must be transported away
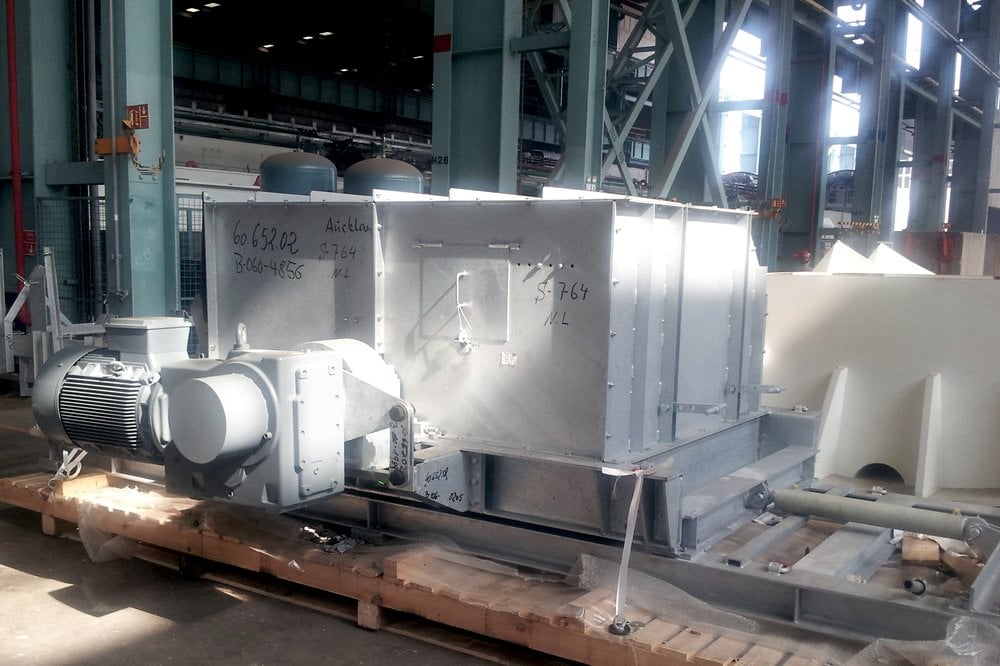
Illustration 3: NORD DRIVESYSTEMS supplied the drives for the conveyor belts demanding transportation.
Demanding transportation task
Below the center center, and being bored in parallel, the TBMs excavate up to 1,300 tons of “London clay” per hour in the two 20 ft diameter tunnels. The handling of this soft material does require solutions that are tailored to the soils consistency. In this case, the challenge lies in reliably transporting the excavated material away from the building site, which includes routing it over machine, tunnel, and hall conveyors before loading it onto trains. State-of-the-art tunneling includes the technology to excavate material directly at the boring machines in order to facilitate handling. However, if the special London clay formation and these additives came into contact with standard conveyors, complications would soon arise: the mass would promptly and persistently stick to parts of the conveyor belts. Tunnel conveyors for the “London Crossrail” project were therefore custom-tailored by the Herrenknecht subsidiary, H+E Logistik. In addition to special plastic coatings and other measures, a wiper system developed especially for the on-site requirements serves to prevent problems caused by conveyed material sticking to exposed system components.
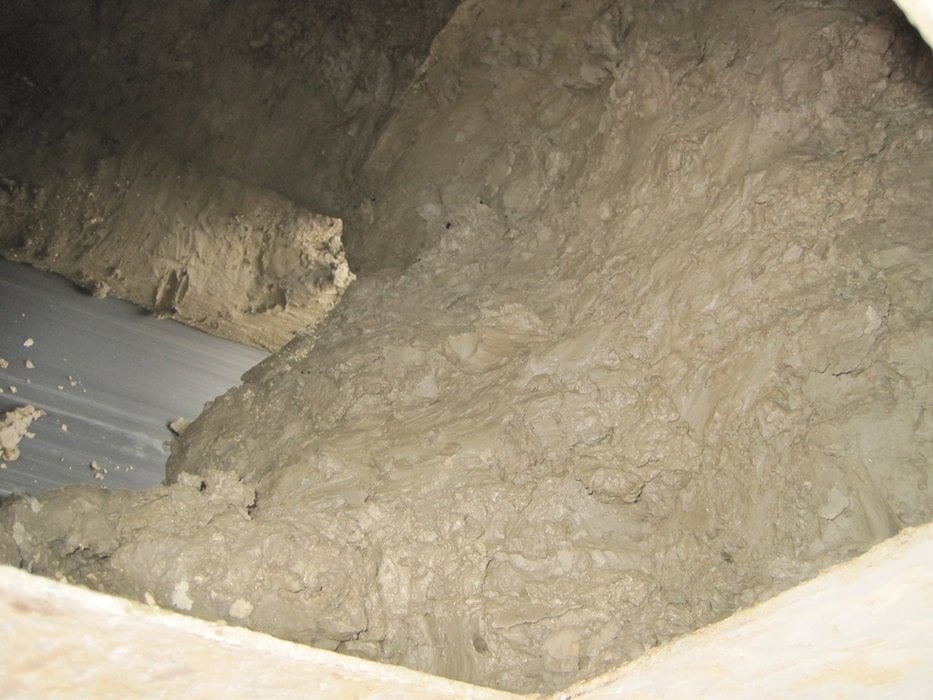
Illustration 4: The TBMs easily penetrate the clay soil found in London which poses a special
challenge for the conveying technology
Reliable and versatile
H+E Logistick, specifying and demanding reliable conveying drive technologyapproached its proven partner, NORD DRIVESYSTEMS from Bargteheide, near Hamburg.“We have been cooperating with NORD for approximately ten years now, and together, have tackled hundreds of projects" says Dirk Uphues, the H+E project manager. Dirk, who is in charge of the London operation, continues:
“The reliability of geared motors on our conveyors has always been a decisive factor. NORD fulfills this key requirement, no matter which drive type they deliver for us.” For the London tunnel conveyors, NORD supplies helical bevel geared motors with a double-sided, smooth output shaft. An expansion coupling transfers the torque to the belt conveyor. “Of course we would like to minimize the drive variety, and the double-sided shaft allows for the versatility that we need. Our systems typically complete not only a single tunneling project, but are often bought back on completion for other tasks. With a variable drive configuration, they can more easily be used in different locations”, says Uphues.
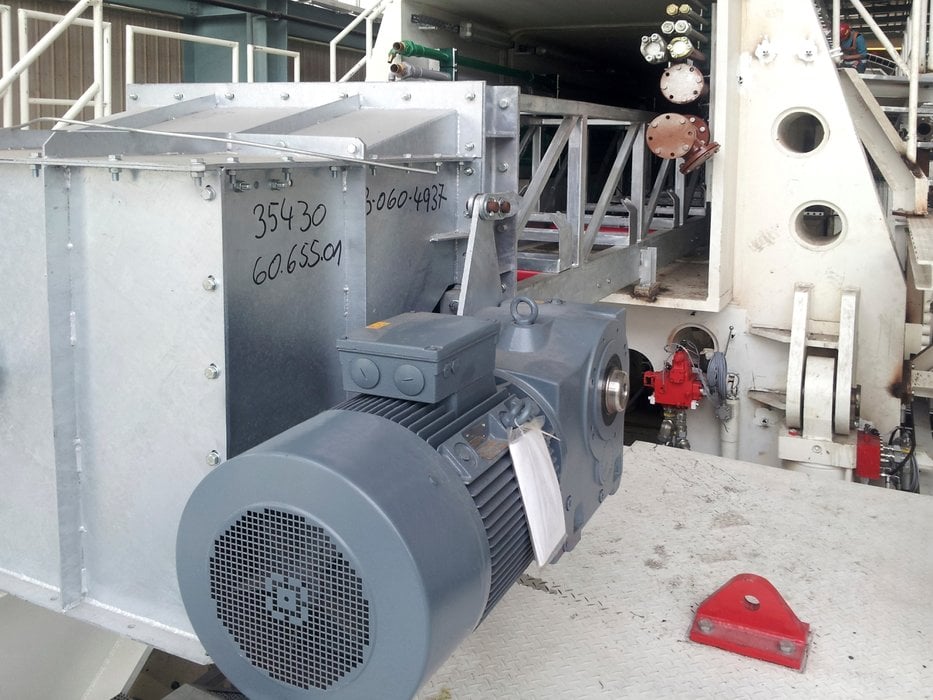
Illustration 5: NORD DRIVESYSTEMS inventory turns, promises their customers availabilty and versatility.
All NORD gearbox housings are manufactured using a single piece construction (UNICASE) with no joints or seams. This ones step process even applies to the very powerful large industrial gear units, rated up to and over 2 million lb-in. which are required for extreme conveyor inclines and moving very large amounts of conveyed material. The one-piece UNICASE housings of NORD’s industrial gear units feature integrated bearing seats. Thus, there are no sealing surfaces between the drive side and the gearbox housing that are susceptible to damage through torque and radial forces. With its offset bearing shaft arrangement, the UNICASE design also ensures very compact dimensions allowing for the use of larger bearings for higher loads and extended working life. Industrial gear units can be installed as left or right side conveyor drives and most types are globally available with fast delivery times. Even though tunneling projects can take many years, customers like H+E Logistik appreciate suppliers who can ensure short-term availability. Besides tunneling, the London Crossrail project also includes the remodeling of existing stations and the construction of new ones. Some time ago, additional manual excavation work that could not be planned in advance near Bond Street Station was scheduled on short notice. So as not to affect other project deadlines, H+E was tasked with providing suitable short conveyors within eight weeks. “The required drive technology from NORD arrived five days after ordering”, says Birgit Barian from the H+E purchasing department. “Particularly when a project is nearing completion, you can easily find yourself in a situation with tight delivery deadlines and considerable time pressure. Even if you have kept all of your own deadlines, many third party problems and sometimes unforeseen circumstances come into play. Without partners like NORD, that are available virtually on demand, you may easily find yourself in difficulty.”