www.magazine-industry-usa.com
16
'20
Written on Modified on
Substantial Time and Cost Savings in the Maintenance Management of Production Tools due to Holistic System Integration
The Manufacturing Execution System (MES) ZEISS GUARDUS and ZEISS Reverse Engineering work hand in hand.
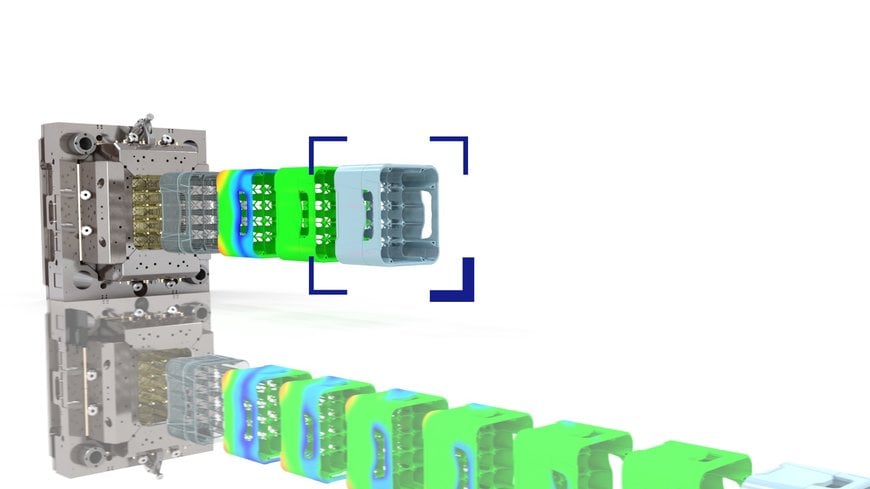
The efficient interaction of ZEISS GUARDUS and ZEISS Reverse Engineering (ZRE) accelerates not only the processes and correction loops in tool maintenance and tool construction. The real-time knowledge of the MES regarding the quality state of the manufactured parts as well as the possible wear of the production tool offers the potential of organising the process between tool maintenance and production in an obviously more efficient way.
The software ZEISS Reverse Engineering is a performant tool for the so-called reverse engineering process. Moreover, it offers specialised functions for the quick and easy correction of injection mould tools. These functions are especially used in the pilot production as well as for the repair of already worn tools. It is exactly this area where it is very important to correct the tools as quickly as possible so that the series production of “good” parts can be started or continued. The correction is carried out within ZEISS Reverse Engineering with three real data records: the CAD model of the tool, the CAD model of the product and the measured real data (e.g. point clouds or polygon meshes) of the manufactured plastic part as well as the measured real data of the used or worn tool.
The result of the correction resulting from the algorithm and the user entries is an updated CAD model based on which the tool will be subsequently adjusted by eroding or milling, for example. The successful use of the software and adjustment of the tool enable a reduction of the correction loops by up to 50 per cent.
The ZEISS GUARDUS users can also increase the efficiency within this process. The foundation for this is the integrated database of the MES of all the quality and production relevant product and process data in real-time as well as information about the setting up of production facilities, that is, the attachment of adequate tools to the machine and its calibration to the planned manufacturing order. During the production, the MES collects all the data which are important for the maintenance intervals and further correction of the tool, such as the manufactured piece number, cycles as well as information about the end of the production order and the stripping down of the machine.
The ‘last part’ of the production order is sent to the testing laboratory for approval. When measuring this ‘sample’, the person responsible for quality assurance checks not only the product characteristics defined in the customer order but also indicators which inform about the current wear of the tool. This concentrated expertise of the MES enables you to analyse the worn areas via a false-colour image within the ZEISS Reverse Engineering and to correct them, if necessary. The maintenance management subsequently decides without any effort to obtain more information whether rework is required or whether the following production order can still be manufactured without any quality deviations. Therefore, the loop between the product and tool as well as between construction and production is closed.
www.zeiss.com