www.magazine-industry-usa.com
03
'13
Written on Modified on
Italy’s only private brewery builds Europe’s most modern brew house: NORD DRIVESYSTEMS supplies powerful drives
During 40 years of continuous around-the-clock operation, the tanks and vats in the Forst specialty beer brewery’s old brew house produced 25 million hectoliters of beer. Now, since brewing technology has progressed, especially with regard to energy aspects, the management decided to build a completely new brew house which was to operate highly efficiently, comply with the latest safety requirements, and produce the lowest possible emissions. The brewery in Algund, South Tirol, commissioned leading German companies to construct five large vats, complete with brewing technology and piping systems, a newly designed water supply, a malting plant with twelve silos, and three separate storage vats. NORD DRIVESYSTEMS custom-tailored all necessary drive units.
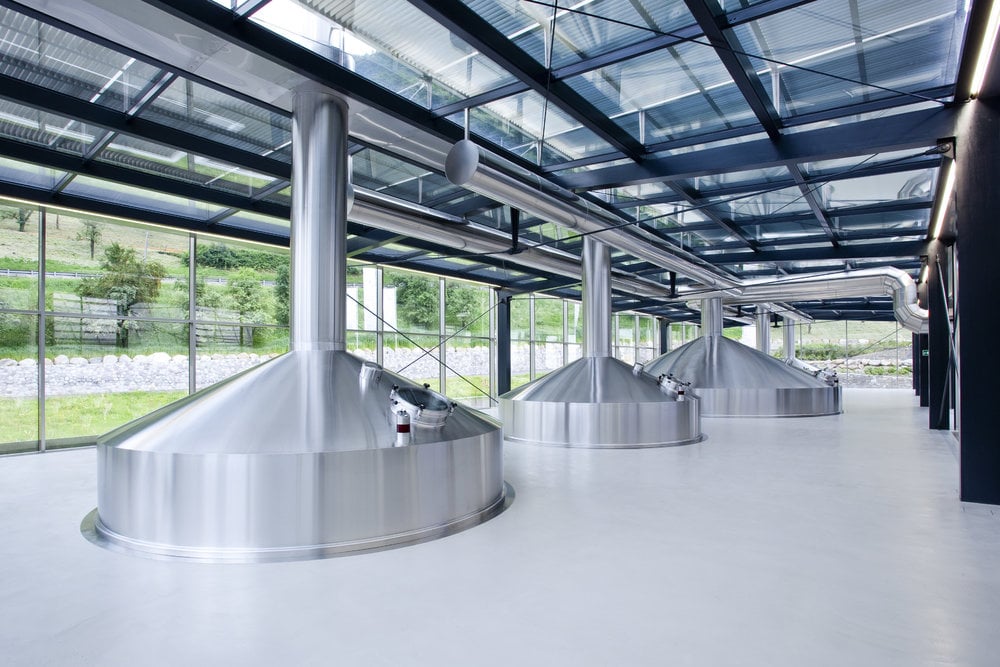
With a 156 year tradition, Forst is a well-renowned name in beer brewing in Italy. The new brew house is located at the perimeter of the extensive brewery premises and can easily be seen from the road passing by. It is a landmark with its distinctive 4,800 m² glass façade. Up to twelve brews per day can be produced here, each with a volume of 630 hectoliters. The annual production capacity is 900,000 hl.
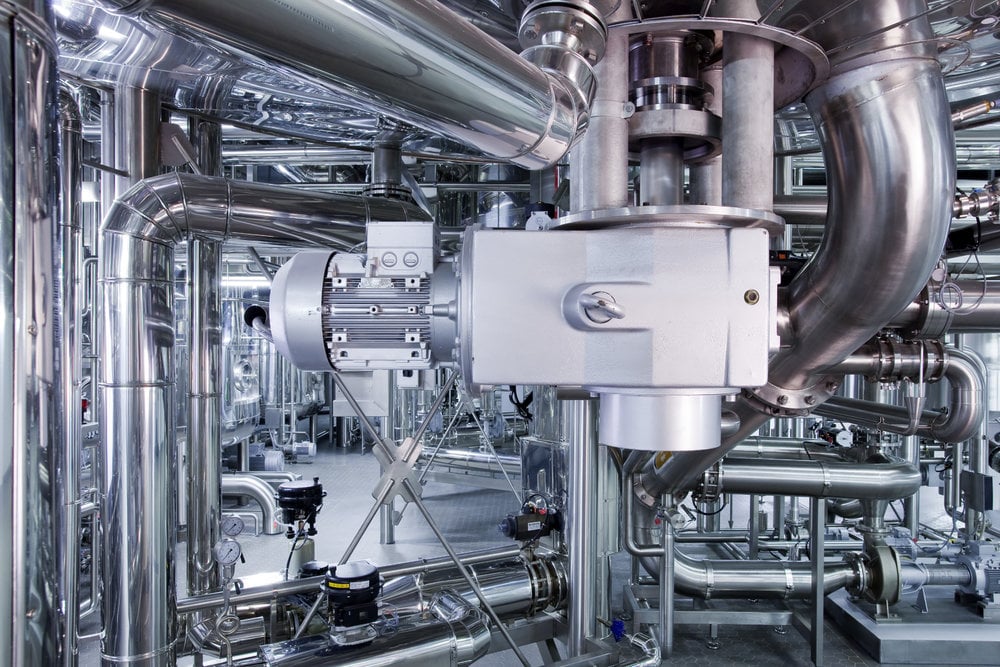
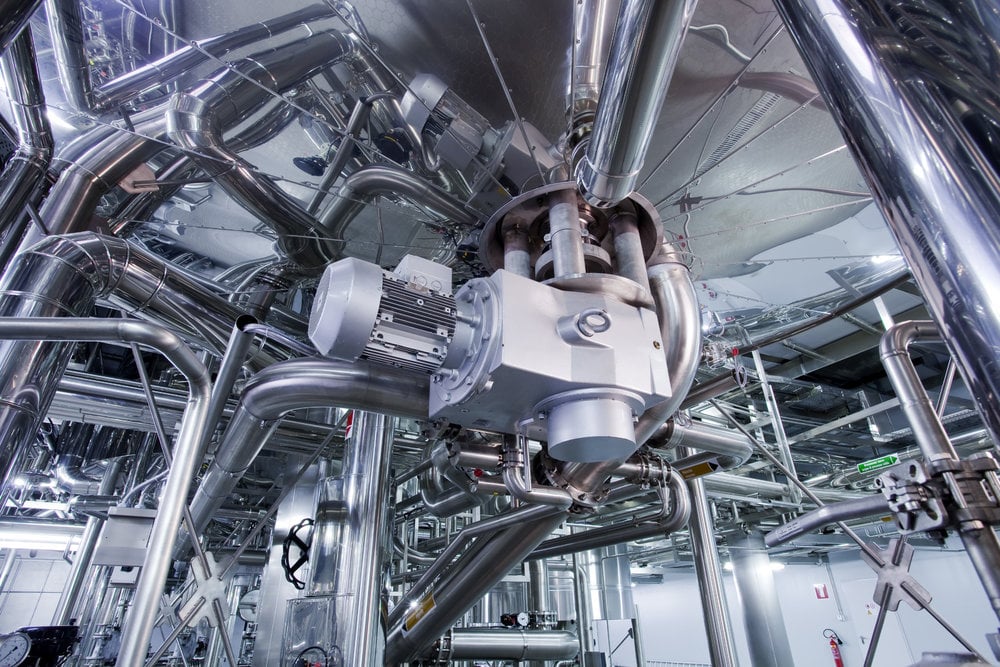
Illustrations 2, 3: Each drive unit was tailored to the individual requirements of the application, pictured: a helical bevel gear motor powering the mash tun.
Trouble-free transition to the new facilities
The engineers and technicians had just 16 months to construct the main components from scratch. “The tight schedule was the greatest challenge with such a complex and technically sophisticated plant”, says Werner Würth, Development Engineer at Ziemann International GmbH. The general contractor specializing in breweries was responsible for the planning and construction of the brewing equipment. The five brewing vessels and the machinery were manufactured in the Ziemann factory in Bürgstadt/Main from where they travelled the 550 km to South Tirol on trucks. During construction the actual brewing process had to continue as usual. Even the transition to the new plant had to take place without any interruption to production.
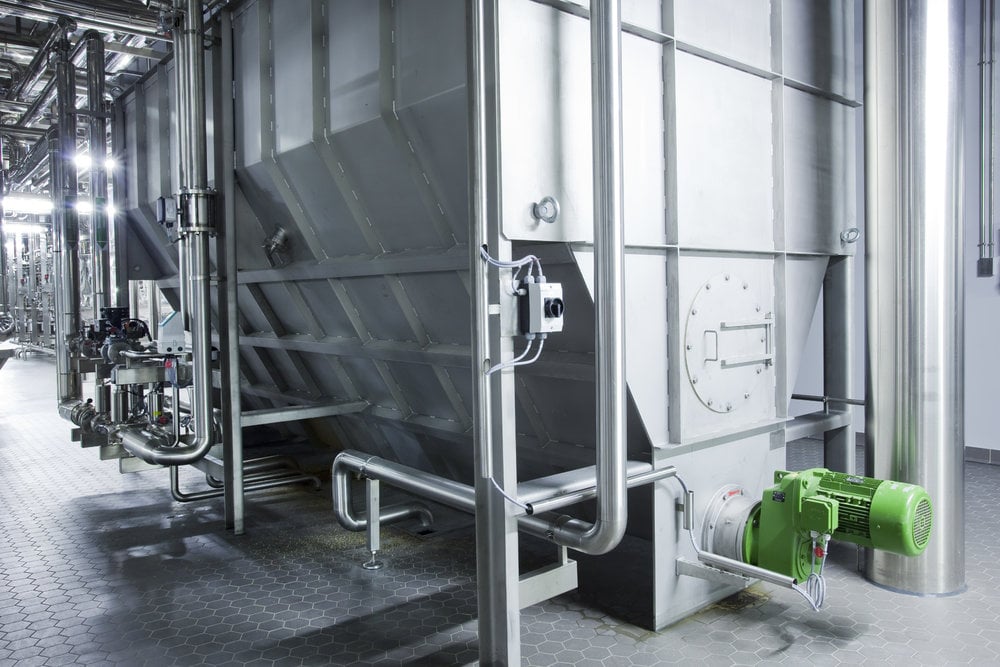
Illustration 4: A parallel shaft gear unit drives the screw conveyor removing the spent grain.
Each drive unit tailored to its task
NORD DRIVESYSTEMS assembled the geared motors for all the vessels according to the specific requirements of the various applications, from the grinding mill, which gently grinds the malt at the start of the brewing process, to the screw conveyor removing the spent grain. In the first stage of the process the malt is mixed with spring water from the nearby mountains in the mash tuns. The mixture is then heated to various temperatures by means of thermally optimized conducting surfaces at the bottom and the frames of the mash tun. A frequency-controlled NORD helical bevel gear motor, equipped with a temperature sensor, drives the agitator inside the vessel. Subsequently, the liquid is pumped into the lauter tun.
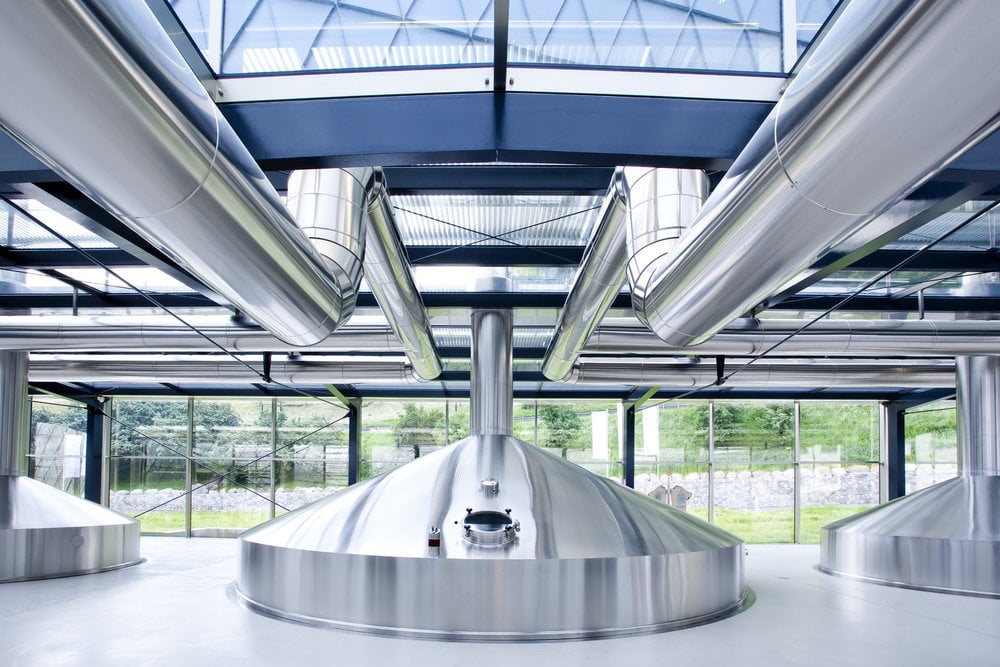
Illustration 5: With an 8.6 meter diameter, the lauter tun is the heart of the brew house. Here, the mash is automatically separated from the spent grain.
Smooth lauter speed adjustment
Measuring 8.6 m in diameter and weighing close to 21.5 t, the lauter tun is the heart of the brew house. The liquid and solid parts of the mash are separated in a fully automated process. As the spent grain settles on the floor of the vat, it forms a natural filter layer. A special raking machine loosens this layer in order to ensure an optimum flow of the beer wort. Thus, the wort quality improves and raw materials are used efficiently. Pressure sensors at the bottom of the vessel detect the spent grain’s consistency, and the drive adjusts the machine’s speed accordingly. “This intelligent control system enables flow rates between 9 and 14 liters per minute and square meter”, says Würth. Next, the spent grain is removed: the machine is gradually lowered and the flat bars mounted on its six arms push the spent grain out of the tun through a hatch. This step is also fully automatic. If too much mass accumulates, the lowering process stops, and the speed is adjusted. Thus, the tun can be emptied in as little as six minutes. In order to process the material as gently as possible, the spent grain is loosened at low speed. But when the spent grain is removed, high speeds are required so the vessel can be emptied as quickly as possible. “Thus, the clouding of the spent grain is minimal, and the flow is very efficient”, Würth explains. Both tasks are handled by a custom-tailored NORD drive unit based on a splined hollow shaft. The drive is a combination of a motor, an industrial gear unit, and a helical bevel gear unit. It has a maximum torque of 96,000 Nm and can continuously regulate the circumferential speed from one to one hundred meters per minute – while providing a constant torque. Würth says, “To check whether the system is running smoothly, the speeds, current consumption, and the motor temperature are centrally monitored continuously.”
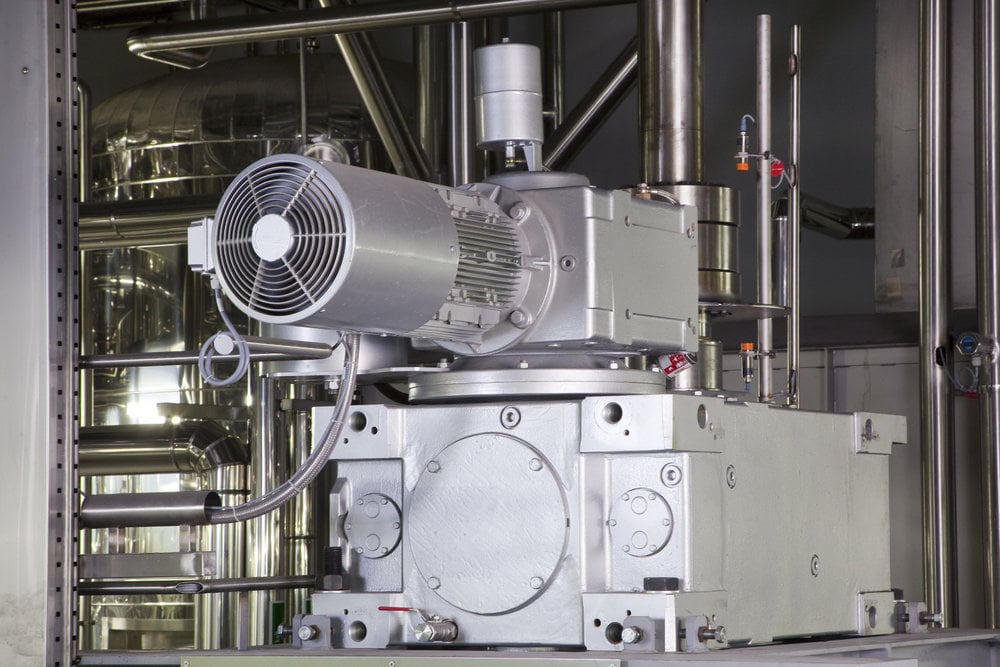
Illustration 6: A single drive unit actuates the lautering process, both loosening the spent grain and clearing out the tun. The combination of geared motor and industrial gearbox achieves torques of up to 96,000 Nm.
Accurate to the millimeter
Inside the lauter tun, the raking machine is lifted and lowered by up to 500 mm. The lifting device works accurately to the millimeter, even under full load. A limit switch and an optical sensor were installed for exact positioning. The height can be adjusted during standstill, in an idle phase, and during operation. To this end, both the helical gear unit and the oil-hydraulic lifting unit are designed to withstand the axial and radial loads which occur in the process. The drive motor has an 18.5 kW power rating and provides output speeds of 0.04 to 4 rpm. To ensure that the required speed is maintained, the motor has been equipped with an encoder. An external fan cools the motor at low speeds. Both gear units feature oil expansion tanks to prevent lubricants leaking from the vent valves at high temperatures. A special sealing system on the industrial gear unit ensures that there is always an adequate lubricant film on the shaft. Due to the design, the lifting cage does not require additional oil reservoirs, which eliminates the problem of sealing. Following the UNICASE principle developed by NORD, all the bearings are integrated into a single housing block which provides excellent strength and rigidity. UNICASE gear cases have no sealing surfaces that could deflect under the effect of torque or radial forces. The compact and light gear units run very quietly and have a longer service life and lower energy consumption than models with multiple-part housings.
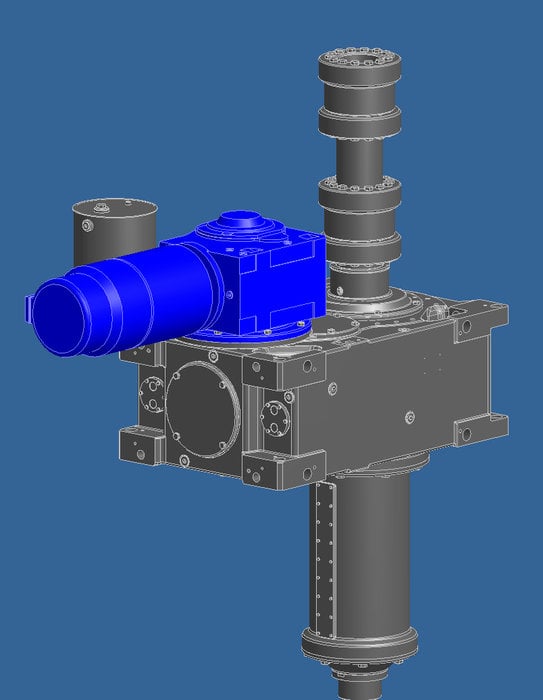
Illustration 7: The helical bevel gear motor is combined with an industrial gear unit based on a splined hollow shaft.
Modern technology reduces steam consumption by 47 percent
The project stands out not only because of its size and the modern architecture. Dr. Walther Unterthurner, Technical Director at the Forst brewery, points out, “Constructing the new brew house, we wanted to ensure that the resources would be processed as gently as possible. Furthermore, we wanted to use these modern technologies to considerably reduce energy consumption and emissions.” Therefore, in addition to efficient facilities in the brew house, a new heat recovery system has been integrated into the vapor condenser. The heat required for the production of the beer wort is stored in a large energy reservoir in the form of hot water tanks at the rear of the building and is reused for subsequent brewing processes. According to Unterthurner, these various measures have already reduced the consumption of primary energy by 30 %. “Our target is to reduce steam consumption by at least 47 %”, he adds.
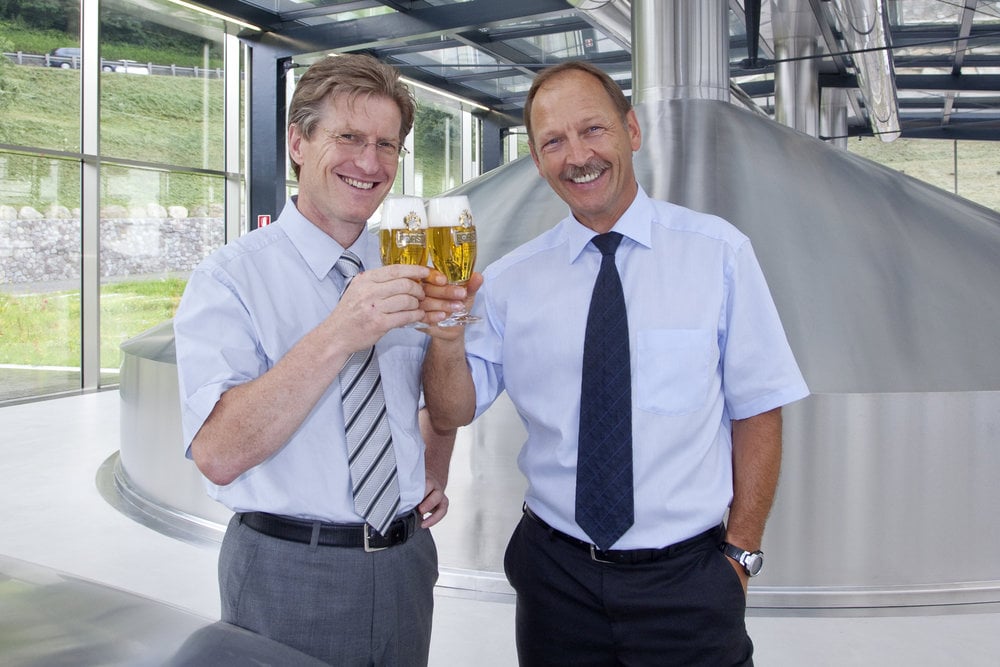
Illustration 8: “The new brew house is a showpiece project designed to operate reliably for at least 40 years”, says Dr. Walter Unterthurner, Technical Director at the Forst brewery (left; with Master Brewer Manfred Biechl).
Conclusion
“The new brew house is designed to operate reliably for at least 40 years”, says Dr. Walter Unterthurner, Technical Director at the Forst brewery. NORD DRIVESYSTEMS technology plays an important part in this. Due to the modular concept of housings and gear components, the drive units were custom-tailored to the requirements of the brewery, contributing to time savings and efficiency improvements. The new brew house is considered a model of modern European brewing. In the very first week after start-up, Forst reduced its primary energy consumption by 30 %.