www.magazine-industry-usa.com
20
'20
Written on Modified on
HeavyDuty encoders in demanding conveyance tasks
Open pit excavators and spreaders are real giants among machinery. Every day they do the hardest work under extreme conditions - dust, dirt, rain, heat. A great strain also imposed on the rotary encoders, which are responsible for speed control of conveyor belts. Many manufacturers therefore rely on HeavyDuty encoders from Baumer Hübner. What does it take for encoders to deserve the hallmark "HeavyDuty"?
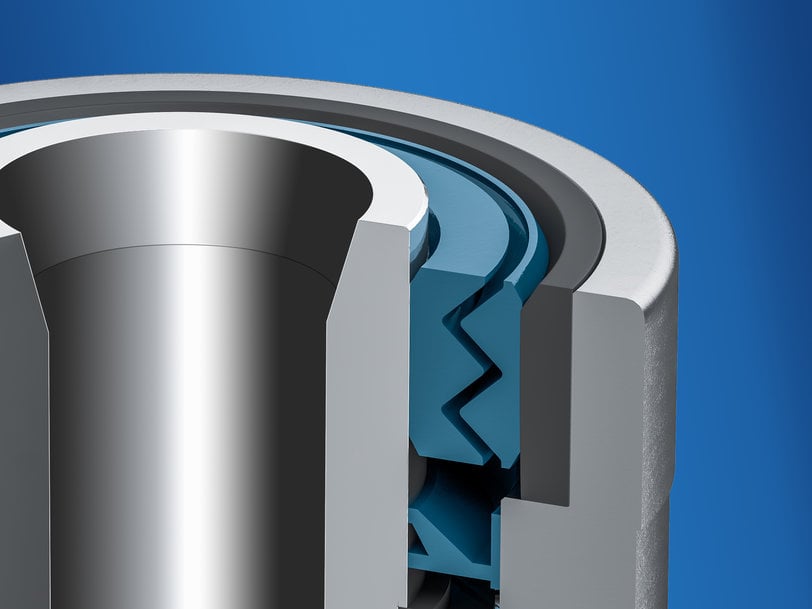
Picture:The ingenious Baumer HeavyDuty sealing concept ensures IP 66 and IP 67 protection over a wide temperature range up to +95 °C. The sophisticated combination of labyrinth and shaft seals permanently protects the HeavyDuty encoders against all types of solids, moist and contamination by adherence.
002_Baumer_HeavyDuty_Dichtung.jpg
Minera El Abra is an open pit copper mine, located 75.6 kilometers northeast of the Chilean city of Calama. Mine output per day are more than 200,000 tons of copper ore for copper cathode production. Conveyor belts transporting the ore over many kilometres must deliver maximum performance. For doing so, they are driven by powerful electric motors. HeavyDuty incremental encoders HOG 10 by Baumer Hübner are ideal for motor speed feedback in a such a demanding outdoor application. They endure dust, dirt, vibration and other harmful impacts that are every-day occurencies in open pit mines. 10,000 kilometres away, at the port of Rotterdam, brother model POG 10 is on duty: In the largest port of Europe, more than 300 million tons of bulk cargo are handled every year, including more than 55 million tons of iron ore and coal. These intermediately stored goods are handled with bucket wheel excavators with a capacity of 5,000 tons per hour. HeavyDuty encoders by Baumer Hübner were chosen for this application because they withstand salty air, rain and frost without any problem. These are just two examples of how HeavyDuty encoders have proven themselves in tough and challenging tasks for many years.
„HeavyDuty“ – precision under heavy load
The English term "HeavyDuty" means extremely resilient, so HeavyDuty encoders are said to be particularly robust. But that's only part of the story and not simply refers to robustness. The term implicates the promise that such encoders will reliably and precisely perform over a long period of time without ever letting users down. For this, HeavyDuty encoders must meet several criteria:
Precision is a focal point. Anyone believing these encoder heavyweights could afford compromising in this point is on the wrong track. On the contrary, HeavyDuty encoders must deliver the same precision signals as their little brothers. Plant control systems utilize these signals for speed monitoring at drives or position feedback at machine parts. To controllers, this is the only way to “get informed” of any excess speed or the drive falling below a defined speed limit so they can intervene accordingly. Even minor measuring errors can have drastic consequences that may result system damage, e.g. in bulk material conveyance.
Robust technology for maximum sytem uptime
Besides precision, reliability is likewise important – as shown in the examples of open pit mining and bulk material transport. For reliable performance in the harsh conditions present in open pit mines and port installations, the encoders must withstand hard shocks, vibration and other shaft impacts without losing their precision capabilities for many years. Product exchange is expensive, not because of encoder pricing but because of installation in places difficult to access and system downtime for the time of exchange. Robust, thick-walled housings and a shock and vibration resistant interior are basic requirements. In addition to that, Baumer Hübner encoders provide generously dimensioned bearings with large bearing spacing at both shaft ends.
Not only mechanical robustness but also electrical resilience is a must. For example, if electromechanical fields generated by live, unshielded cables are present close to the encoder. Without appropriate shielding, the encoder electronics may be destroyed or at least be impaired at an extent resulting in measuring signals of bad quality. Shafts currents generated by voltage difference may burn the bearing lubration and lead to bearing damage or destruction. Electrical isolation is therefore indispensable for HeavyDuty encoders.
Tightness is another must. Whether moisture, dust or dirt - HeavyDuty encoders must be well sealed. This is especially important at critical, neuralgic points: shaft and electrical connections. Sealing includes corrosion protection by appropriate materials and coatings, against ingressing salt water and chemicals that would impair encoder functionality.
Original HeavyDuty encoders
"HeavyDuty" is neither a protected concept nor a standard but has become an established term on the encoder market. Inventor of this special encoder class is the world market leader Baumer Hübner with HeavyDuty encoder expertise dating back to the 1950s. This knowhow and experience have incorporated into the development of HOG 10 considered to be the "original" for more than 25 years and the blueprint for every HeavyDuty encoder. Baumer Hübner HeavyDuty encoders not only excel by precision, reliability and durability, but also by the wide selecton of product variants with varied mechanical, electrical and functional options. Incremental and absolute encoders are available in 58 mm housings and as large designs with 287 mm flange size and 150 mm hollow shaft. Baumer Hübner encoders support all relevant analog and digital interfaces. High power outputs ensure excellent and noise-immune signal quality even over long a distance - depending on the product variant up to 550 meters, in fiber optic transmission even up to 1.5 kilometers.
To ensure fail-free operation, electrical functionalities and signal quality undergo 100 percent inspections at Baumer Hübner. Comprehensive quality certificates certify customers absolute encoder reliability. No matter whether copper mining in Chile or bulk materials handling and transport in the port of Rotterdam, HeavyDuty encoders by Baumer Hübner ensure permanent operation reliability without downtime. Even under the toughest conditions.
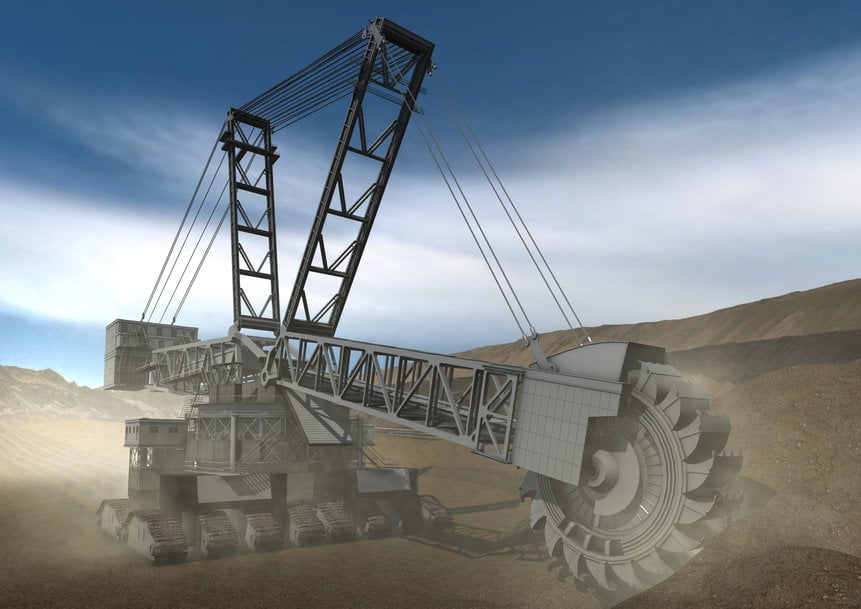
Picture: In open pit mines, HeavyDuty encoders by Baumer Hübner have been proving themselves over and over. Their robust design and double-sided bearing setup ensures maintenance-free operation and a long service life even under severe loads and in adverse environments.
002_Baumer_HeavyDuty_DiggingMachine.jpg
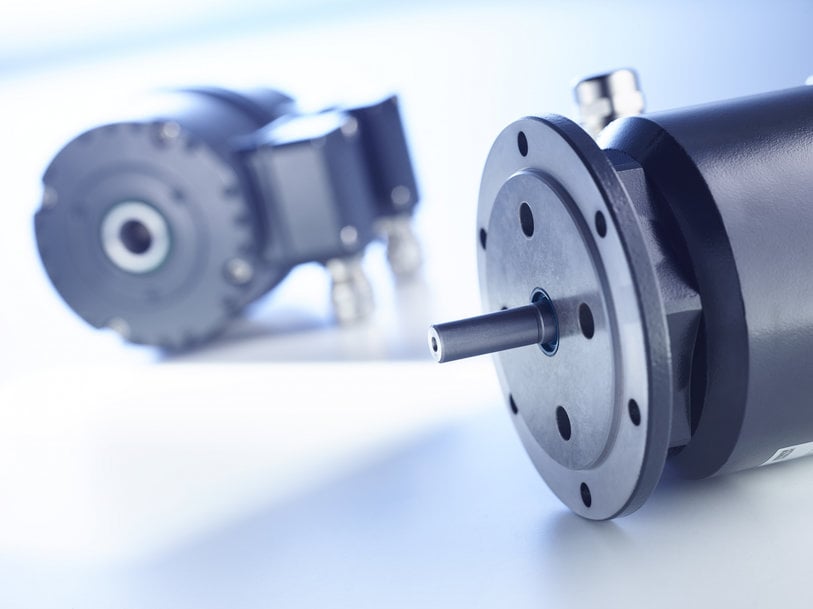
Picture: Incremental HeavyDuty encoders of the HOG10 / POG10 series ensure reliable 24/7 operation even under the toughest conditions. Their resilient, extremely resistant housing, outstanding corrosion protection and longterm stability in the sealing concept ensures fail-free operation in any environment.
002_Baumer_HeavyDuty_PG10.jpg