www.magazine-industry-usa.com
04
'20
Written on Modified on
The Journey Towards Autonomous Manufacturing
Within the industrial world, leaders are defining their journey to autonomous manufacturing. Manufacturers are focusing on digitization strategies that will help to drive efficiency across their plants. As data is increasingly aggregated across manufacturing lines, the reality of autonomous lines is likely to be reached in the next five years.
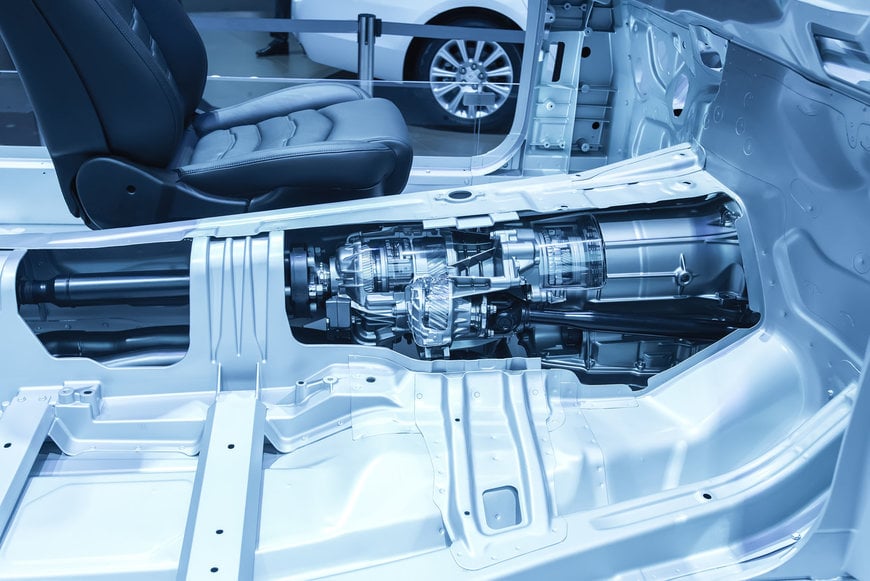
This paper explores the journey towards autonomous manufacturing—what a typical journey looks like and best practices for how manufacturers can begin to achieve this.
A review of production systems in Industry 4.0
When reflecting on the concepts of Industry 4.0, we need to consider where production systems have come from and the changes that have been made over time to improve throughput and efficiency.
Production improvement starts with robotic process automation (RPA), where you take a repetitive process and apply some form of mechanization to improve the throughput rate. The interesting thing here is that it doesn't improve the processes quality, but does make it less variable—simply because the process is more repeatable. For example, if your current process produces 1,000 defects, RPA will make 10 times as many defects, but also produce 10 times as many good parts. This is great for throughput but not very effective for improving quality.
Once manufacturers started shifting paradigms to become more data-led in their production systems (by using historians, PLCs, etc.), it enabled them to draw on that data to inform the expert analysis of the process. This results in improved control limits and a reduction in the variance and in the number of quality defects. It does however make the operators’ job more difficult, as they need to manually maintain the process within these finite control bounds.
The next level of improvement is to make these adaptive changes as quickly as possible, with an understanding of the system from start to finish, to improve production. This final step brings us closer to the goal of autonomous manufacturing. Production systems need to be flexible to tolerate the variance in upstream processes, without compromising on the quality of the final output.
The future of industry 4.0 is definitely much more flexible. We’re at a point where artificial intelligence (AI) systems are able to correct at the highest rate possible, which is ahead of real-time, to produce the best quality at the lowest cost, without the need for a human expert.
The state of autonomous manufacturing today
The journey to autonomous manufacturing is complicated. It's not as trivial as simply turning on a solution. In the final step described previously, the AI solution needs to offer guidance, making corrective suggestions to the production team to improve quality. This helps to reduce the manufacturing risk because the quality result is assured despite a large variance in input material. Total system efficiency is improved because less scrap means greater production capacity, as well as the production of better quality parts.
Most plants today draw data from their production systems and send it to their engineering or production teams. Operators are left to follow their own inquisitiveness as they look through the data to devise an optimization or system improvement. There isn’t a holistic view or use of data from the start to the end of a process to achieve an overall system improvement.
These data led investigations are also limited by the complexity of the manufacturing system. These systems-of-processes are often too complex to express in the terms of classical engineering descriptions of their processes. An engineering model that would be able to handle material from the start of the process through to the finished goods is too complex to express analytically or interrogate with traditional methods. In addition, the traceability of the component through a complex process is very difficult to achieve. Unless the system achieves an incredibly rigorous sampling and tracking of the component flow, people alone are not able to join the data from step A through to step Z.
The solution to this complexity is an Expert Execution System (EES) that allows manufacturers to express the relationship between the start of a process and the end of the process, without having to enforce the rigorous traceability that would typically be required. This system requires looking at the process with a slightly different view. It’s important to understand the quality result from each step in the process to make a final quality improvement at the end of the process.
Existing systems can be used
The paradigm of autonomous manufacturing is specifically designed to work with existing processes. The only change is that the manufacturing system becomes more data-led, by using production data and quality data to make the prescribed process changes that result in improved quality. The journey to autonomous manufacturing is, in fact, predicated on having an existing production system - although it can also work in greenfield spaces. Autonomous manufacturing only requires enough data to describe the process in order to make a substantial impact on the system.
The shift from reactive to prescriptive AI
In reactive manufacturing, a quality failure is discovered at the end of the line and the production team will make a set of reactive changes to the system to correct for the immediately observed error. This approach has two core features: the first is that the defect has already occurred and the second is that the factory keeps producing poor quality goods until the root cause has been solved. A prescriptive system is very different, as it involves making a small change now to avoid future quality failures. A small set of corrective actions are made in anticipation of a quality cost that is never realized. These prescriptions can help to reduce the cost of non-quality. In the reactive case, by contrast, one waits for the quality failure and all the associated costs to occur before correcting the failures in the system.
Best practices for autonomous manufacturing
The two most important things manufacturers can do to prepare production systems to achieve the goal of autonomous manufacturing are:
-Identify and save production data. As soon as a plant can start saving production data, it opens the opportunity to use that data to optimize the future. That’s the single most important thing manufacturers can do now if they haven’t yet started.
-Improve the quality system. To improve quality, it’s important to ensure that the details of the defect are recorded (type, location, and description), and not just the fact that a defect has occurred. This will allow AI to automatically diagnose the root cause of the problem and to provide continuous directions - to the machine or to the operator—so as to improve quality.
Dr. Michael Grant, CTO, DataProphet
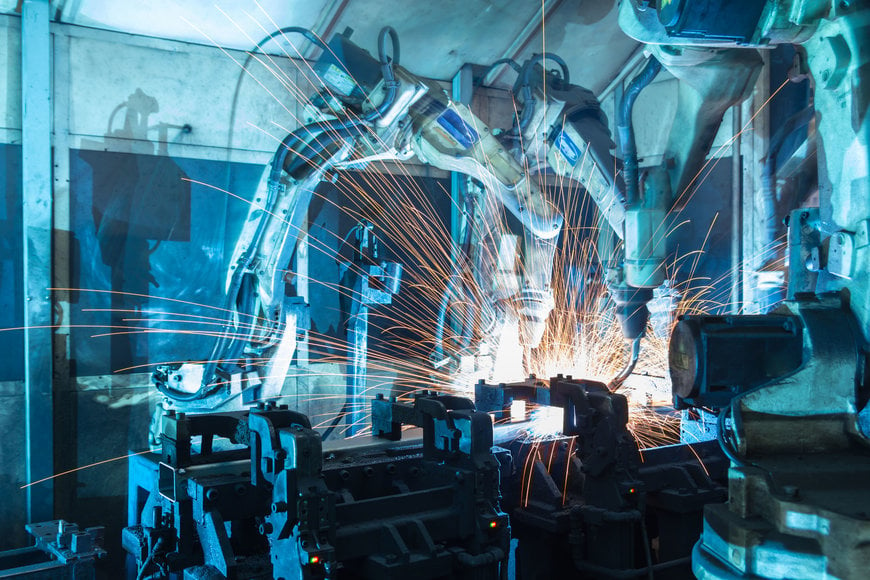