www.magazine-industry-usa.com
10
'12
Written on Modified on
Kennametal Launches Beyond Blast™
Game-changing interface of tooling and coolant delivers outstanding tool life and productivity improvements
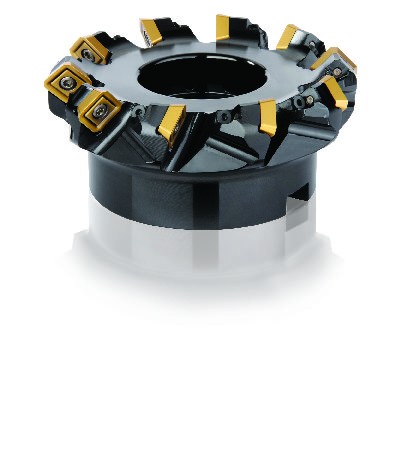
Now, Kennametal is taking another giant step forward with Beyond Blast™. By channeling coolant through the insert, at the interface of the milling cutter and insert, Beyond BLAST delivers coolant directly where the tool cuts the material, ensuring more efficient coolant delivery, heat transfer, and lubricity.
Addressing Friction Improves Cutting
Maximizing a company’s milling productivity and reducing manufacturing costs means improving speeds (sfm/Vc) and feeds to achieve maximum metal removal (MMR).
Intelligent coolant application is key. Mechanical cutting generates frictional heat. At high cutting speeds, the rate at which heat is absorbed by the tool increases with velocity. To optimize their performance, tools must be adequately cooled.
Proper coolant flow means improved tool life and higher maximum effective cutting speeds for a number of reasons. When not properly cooled, the insert will heat up rapidly, which shortens tool life. In many cases, the workpiece can heat up significantly, too. This negatively affects surface finish and dimensional control, causing a failure mode typically called plastic deformation.
Traditional flood coolant jets are uncontrolled and wasteful. This is because they are aimed at the cut, but often hit behind the cutting zone. Instead of making cutting more efficient, this can actually add to problems by pushing chips back into the cut, increasing chip friction and accelerating tool failure due to increased chip recutting. Custom high-pressure systems (1,000 psi or higher) engineered to address this situation can cost tens of thousands of dollars to install and maintain. Even ultra-high systems delivering coolant in excess of 4,000 psi have been observed emerging in specialty applications. With Beyond BLAST™, coolant is delivered through the insert, at the interface of the milling cutter and insert – delivering the best of both worlds.
Test cut graphs show typical cooling applications often miss the point of highest heat, generated where the tool shears the material. Hitting chips after they have formed proves typical cooling applications can even work at cross-purposes by forcing chips back into the cut, accelerating tool wear. Part of the problem is that the coolant-delivering nozzle is located relatively far from the workpiece.
Beyond Blast’s thru-insert cooling delivers coolant much closer to the tool/chip interface. Coolant pressure remains adjustable, but since the coolant is delivered through the insert, coolant delivery is more reliable and controlled, significantly reducing temperatures at the point of the cut.
Beyond Blast is available for both turning and milling applications, each with significant productivity-improving potential. “In tests involving titanium turning, Beyond Blast inserts at 100 psi were showing 75% improvement in tool life over the same inserts with flood coolant at 100 psi,” says Fabricio. “In a different test to evaluate the influence of coolant pressure, tool life for Beyond Blast at 100 psi was nearly that of identical insert geometries at 1,000 psi.
The Beyond3.jpeg drawing shows Beyond Blast indexable milling inserts and the coolant-delivery path through the milling cutter and insert. In milling tests involving titanium (TiAl6V4), results are even more spectacular. Compared to coolant delivery through the spindle, Beyond Blast tool life shows tool life increases of up to 300% depending on the insert geometry and cutting conditions.
“With Beyond Blast, the result gives Kennametal a new and improved turning and milling product portfolio and it’s very easy for metalworking companies to upgrade their manufacturing processes,” says Fabricio. “It’s a plug and play solution.”
Currently, two shell mill families are available with Beyond Blast inserts, the new KSSM 45oЀ and KSRM™. Designed for square Beyond Blast inserts, KSSM 45o shell mills are available in inch or metric versions and also coarse or medium pitch, suitable for a wide variety of materials. KSRM shell mills and indexable end mills are designed for round indexable Beyond Blast inserts and are also available in inch and metric configurations. Drawings, CAD files, and additional technical information are available by visiting www.kennametal.com.
Beyond1.jpeg: Typical flood coolant is undirected and wasteful, and can have a deterrent effect by forcing chips back into the cut.
Beyond2.jpeg: Beyond Blast™ is directed where the cutting edge meets the work material.
Beyond3.jpeg: Beyond Blast indexable milling inserts and the coolant-delivery path through the milling cutter and insert
Beyond4.jpeg: Beyond Blast™ from Kennametal (here shown with KSSM™ shell mill) delivers coolant from the insert, significantly extending tool life and performance.