www.magazine-industry-usa.com
05
'19
Written on Modified on
E4TC at RWTH Aachen Campus determines potential New Study: “Engineering 4.0”
The European 4.0 Transformation Center (E4TC) at RWTH Aachen Campus has investigated the strategic digitization of design and control engineering and the technical layout of machines and plant systems. The 38-page research report titled “Engineering 4.0” is based on an eight-month field study of German machine manufacturers (producing both series products and special machinery), of engineering offices/hardware planners, and of component manufacturers. For the first time, the methodology developed to quantify available potential in engineering and measures to be taken enables a well-founded consideration of current engineering workflows for both series production and special-machinery manufacturing. Its central finding: A partial automation of engineering processes achieves an optimal cost/benefit ratio.
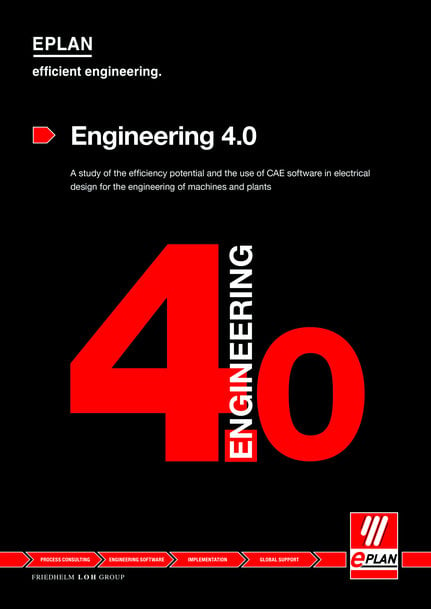
The scientists at E4TC in Aachen, Germany, initially introduced a model of the engineering workflow and created an evaluation matrix with five efficiency levels. The “Efficiency Level” matrix contains detailed descriptions of the methodology/workflow and is accompanied by a “Use Level” matrix, which describes and evaluates the use of CAE software as a basic prerequisite for Engineering 4.0. A total of ten process steps characteristic for engineering in machine manufacturing (series/special machinery) were examined. The engineering workflow model generated comprises the typical work steps of the ordering cycle.
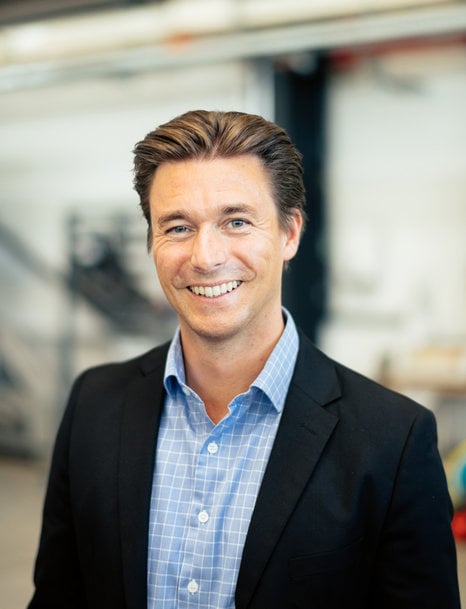
Dr. Thomas Gartzen_E4TC.jpg: “Companies are literally completely in control here to tap into potential time and cost savings through standardization or automation projects,” says E4TC Managing Director Dr Thomas Gartzen.
Engineering workflow model/Efficiency Matrix
The researchers focused on the work fields of engineering, design, bills of materials, reports, control cabinet layout and devices and templates. The reasons for this are clear: “The dependencies on customers or partners in these process steps are sometimes relatively low or non-existent,” says E4TC Managing Director Dr Thomas Gartzen. “Companies are completely in control in these areas to tap into potential time and cost savings through standardization or automation projects.” The path to higher efficiencies in the value chain is mapped out using traditional methods, going from standardization through to automation. To be able to evaluate the efficiency of each work step, the study scaled the workflow methodology in five stages – where the efficiency level (eLevel) of engineering can be located.
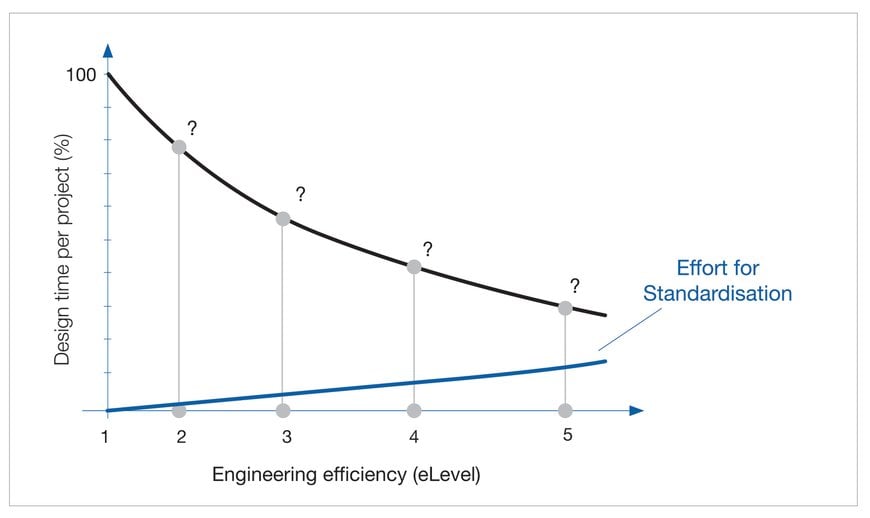
Graphic standardization.jpg: Design time and effort for standardization depending on the engineering method.
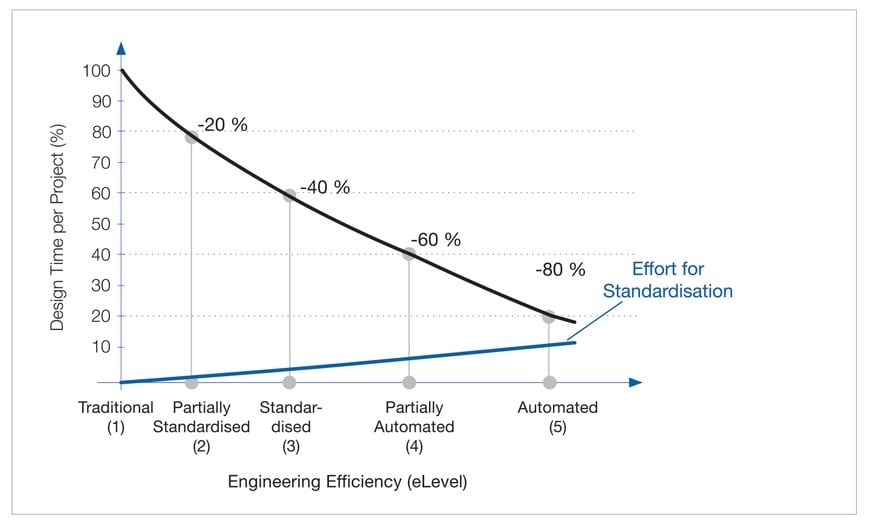
Graphic Engineering Efficiency.jpg: Results: Reference Engineering Efficiency Curve
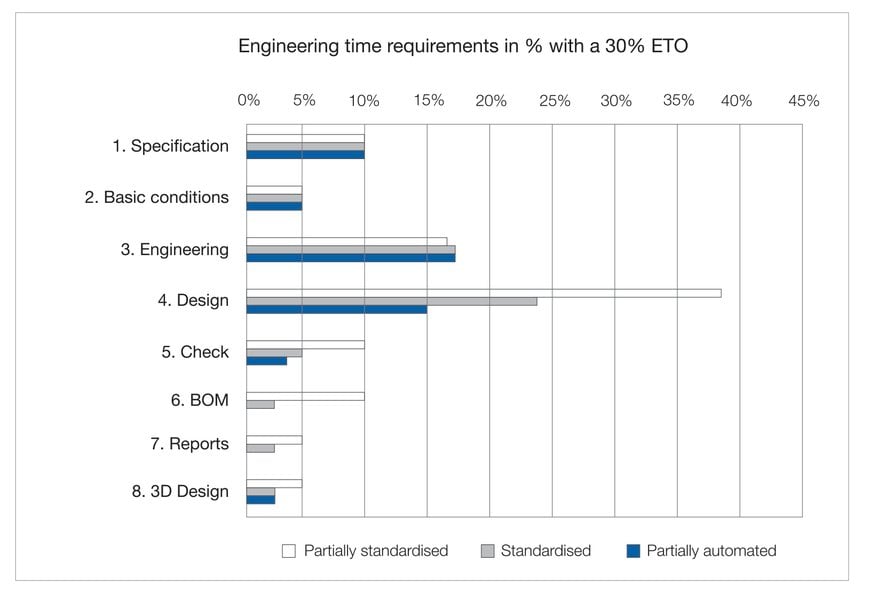
Graphic Engineering Time ETO.jpg: The typical time required for the engineering steps (1–8) in percent, assuming eLevel2.
Increasing potential
Using the collected data, the scientists determined that companies can become 20 percent more efficient from eLevel to eLevel. Device-oriented work methods bring about a 25 percent time savings for schematic creation. Users spent half as much time creating schematics with a circuit library for product functions. Introducing partial automation brings an additional 25 percent time savings for creating schematics and creating all reports is completely eliminated by introducing standardization.
The study can be downloaded free of charge at: http://info.eplanusa.com/explore-engineering-4.0