www.magazine-industry-usa.com
04
'11
Written on Modified on
Testing of electric motors for automotive applications
For its test benches used in both laboratory and in production, Unus International chose the turnkey MEROBEL solution
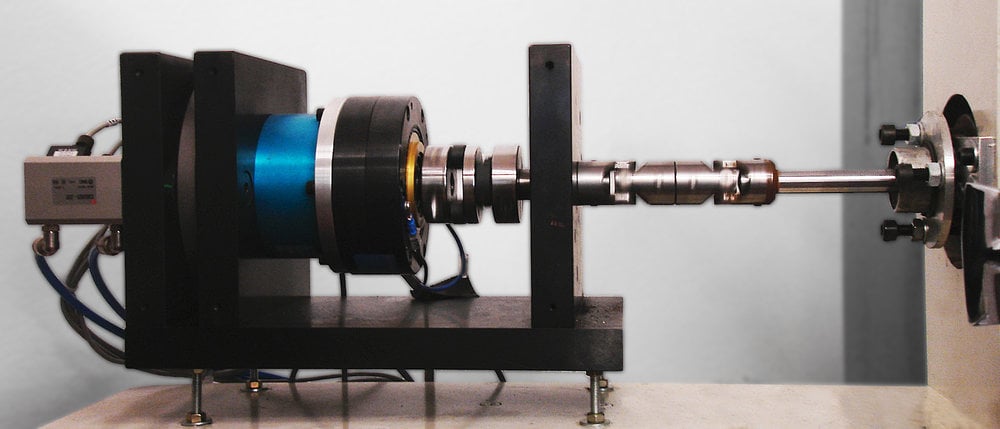
UNUS International manufactures DC motors 12 – 24 - 48 V mainly used as servomechanism equipments for the automotive and the industrial automation industries.
Created in the 70s in Padova, UNUS which was moved in 1995 in Rival di Pianiga (Venice), employs currently about 60 people, with a production of more than 2,000,000 pieces per year.
Including the main following automotive appliance motors and gear motors
- Windows, sunroofs, sunshades, mechanisms
- Seats movement and adjustment
- Steering column;
- Implemented automatic gearbox
The global product range includes also additional motor based equipments for other industries, such as, control of sliding doors, overhead, gates and automation in general.
UNUS International engineers are at the service of customer in developing new projects.
Technical skills and flexibility are the company main values, allowing lower time to be spent in designing, prototyping and manufacturing the initial samplings of new products. This organisation ensures a fast response to a wide range of market needs, with full management of the time-to-market issues.
"Our mission is to offer a product tailored to the needs of the customer, for which the technical level and quality are a crucial issue" said engineer Massimo Melato, Unus International’s General Manager. "At the starting point are our policies on quality and continuously renewed R & D, but also design, production and business organization in general, with the constant target of improving customer satisfaction.”
“Our excellent results, achieved in the domestic and foreign markets with high-tech content products, confirm that we are working in the good direction, while we are continuously improving both our competitiveness and our quality. By the way, UNUS’ motors and gear motors are used as first equipment by major German car manufacturers as well as by the most important automation systems manufacturers"
The strategic importance of testing
Among the reasons for its success, and in addition to the company technological skills, are the high reliability and quality of its production.
UNUS International is among the 100 successful Italian companies mentioned in the 3rd Eurispes report). To ensure such level of excellence, products testing (during production, but also in the laboratory during the design period), gets an absolute strategic importance.
Specialized test benches have been especially set-up for testing 100% of the motors dedicated to automotive industry. "This is primarily for motorized windows, seat moving, canopy opening, adjustable steering column and tendon movement, "says Eng. Melato. "We are currently developing a motor designed to operate the compressor for the pneumatic suspension of the car.
The related test benches were not designed for a particular customer’s application. UNUS has collected all directives from many car manufacturers and has developed versatile test benches able to meet all those specifications.
"Usual solutions found on the market are generally intended to satisfy the widest possible range of applications, "says Eng. Melato, "but in the other hand they are not fully matching the specific needs and tasks we need them to play. Having built the test benches in our own company and having developed its control software by ourselves means they are targeted to our requirements or, rather, the real needs of our customers. "
In the manufacturing process, each motor is tested, both regarding the main working parameters and the noise level. "To proceed with these tests, we have currently 4 testing cabins equipped with MEROBEL brakes, "says Eng. Melato. "The test cycle is 5 and 10 seconds duration, depending on the type of motor, with a daily production of about 8,000 pieces. "
The other test benches are located in the laboratory –where 5 systems are equipped with MEROBEL brakes- in order to check the reliability of the motors and gear motors, through lifetime and fatigue tests.
For such processes, the testing cycle duration is much longer. Some endurance tests, with long cycles and aging simulation through heat cycles in climatic chamber, may take up to 60 days.
These are therefore two very different applications from each other.
"In the laboratory, the tests are mainly dedicated to simulate the working cycle of the motors with different load cycles (ie, with different torque levels) and different environmental conditions (including thermal shocks, temperature range from -40 ° C to 90 ° C and different values of relative humidity) for a certain number of cycles or until the motor’s end of life, "says Eng. Melato. " Then, we use a well-defined duty cycle, according to the specifications of customers". During the motors test duration, each single parameter is constantly monitored and recorded (Current consumption, speed, torque and temperature).
When the motor does not meet the qualifications or does meet a default (eg an overheating, a premature wear of the brushes or the collapse of some component), it is removed for an analysis of the trouble reasons and for applying the needed improvements. After modification, the test is fully repeated for a second time, which leads to get the requested motor quality.
The unique goal is for the motor to meet all customer’s specifications and once it has entered into production to get zero waste.
The same procedure is also used once a year for products tests, in order to check that nothing has changed over the time.
Robust and reliable EMP Brakes – User’s friendly closed loop controllers
To simulate on the test benches the variable load that the motor is supposed to meet during his life, Unus chose a complete solution based on MEROBEL components, with the help of the company’s local subsidiary ANDANTEX SpA.
The chosen components were EMP brakes (type FAT120), torque sensor (type TRS50), and a closed loop controller (type DGT300).
"ANDANTEX advised us about the MEROBEL brakes to be used in this application as well as about the control unit and the various parameters to be set according to our specifications, "says Eng. Melato, "A true partnership was established with ANDANTEX about the supply of the brakes all along the application development. In particular, sharing expertise with our customized software designers, was crucial to get the final test systems fully matching our needs. "
The wide range of solutions offered by MEROBEL includes high-tech actuators such as EMP brakes and clutches, digital controllers, sensors and transducers. The specific know-how acquired by the company allows to offer optimal solutions for almost any kind of variable torque application system, according to its specific requirements.
MEROBEL EMP (ElectroMagnetic Particles) Brakes and Clutches range are made of two concentric rotors, the outside and the inside ones, separated by a gap where are located the magnetic particles.
Variation of the magnetic field in the gap (created by a variable DC current coil fed) leads to a variable “fluidity” of the magnetic particle, and leads to a smooth and variable mechanical coupling between the two rotors (variable torque).
This specific technology guarantees a stable torque, reproducible and independent of the speed of rotation, as well as easily adjustable with a low DC current level.
Among the main features of MEROBEL EMP brakes and clutches, are the proportionality between to the applied current and the provided torque, the independence between torque and speed, the bidirectional operation, very low wear and noiseless operation.
In addition, MEROBEL EMP brakes and clutches are offering low maintenance, fast response time (10 to 50 ms), low electric power consumption, linear response, very easy remote control features, and easy integration in any type of test systems.
"We have been very pleased with the MEROBEL products and the support from ANDANTEX" concluded Eng. Melato. "We had first the MEROBEL Brakes installed at the production test benches. And even if the requests were quite higher, we have now extended the use of these brakes to the laboratory test benches with great success”.
Created in the 70s in Padova, UNUS which was moved in 1995 in Rival di Pianiga (Venice), employs currently about 60 people, with a production of more than 2,000,000 pieces per year.
Including the main following automotive appliance motors and gear motors
- Windows, sunroofs, sunshades, mechanisms
- Seats movement and adjustment
- Steering column;
- Implemented automatic gearbox
The global product range includes also additional motor based equipments for other industries, such as, control of sliding doors, overhead, gates and automation in general.
UNUS International engineers are at the service of customer in developing new projects.
Technical skills and flexibility are the company main values, allowing lower time to be spent in designing, prototyping and manufacturing the initial samplings of new products. This organisation ensures a fast response to a wide range of market needs, with full management of the time-to-market issues.
"Our mission is to offer a product tailored to the needs of the customer, for which the technical level and quality are a crucial issue" said engineer Massimo Melato, Unus International’s General Manager. "At the starting point are our policies on quality and continuously renewed R & D, but also design, production and business organization in general, with the constant target of improving customer satisfaction.”
“Our excellent results, achieved in the domestic and foreign markets with high-tech content products, confirm that we are working in the good direction, while we are continuously improving both our competitiveness and our quality. By the way, UNUS’ motors and gear motors are used as first equipment by major German car manufacturers as well as by the most important automation systems manufacturers"
The strategic importance of testing
Among the reasons for its success, and in addition to the company technological skills, are the high reliability and quality of its production.
UNUS International is among the 100 successful Italian companies mentioned in the 3rd Eurispes report). To ensure such level of excellence, products testing (during production, but also in the laboratory during the design period), gets an absolute strategic importance.
Specialized test benches have been especially set-up for testing 100% of the motors dedicated to automotive industry. "This is primarily for motorized windows, seat moving, canopy opening, adjustable steering column and tendon movement, "says Eng. Melato. "We are currently developing a motor designed to operate the compressor for the pneumatic suspension of the car.
The related test benches were not designed for a particular customer’s application. UNUS has collected all directives from many car manufacturers and has developed versatile test benches able to meet all those specifications.
"Usual solutions found on the market are generally intended to satisfy the widest possible range of applications, "says Eng. Melato, "but in the other hand they are not fully matching the specific needs and tasks we need them to play. Having built the test benches in our own company and having developed its control software by ourselves means they are targeted to our requirements or, rather, the real needs of our customers. "
In the manufacturing process, each motor is tested, both regarding the main working parameters and the noise level. "To proceed with these tests, we have currently 4 testing cabins equipped with MEROBEL brakes, "says Eng. Melato. "The test cycle is 5 and 10 seconds duration, depending on the type of motor, with a daily production of about 8,000 pieces. "
The other test benches are located in the laboratory –where 5 systems are equipped with MEROBEL brakes- in order to check the reliability of the motors and gear motors, through lifetime and fatigue tests.
For such processes, the testing cycle duration is much longer. Some endurance tests, with long cycles and aging simulation through heat cycles in climatic chamber, may take up to 60 days.
These are therefore two very different applications from each other.
"In the laboratory, the tests are mainly dedicated to simulate the working cycle of the motors with different load cycles (ie, with different torque levels) and different environmental conditions (including thermal shocks, temperature range from -40 ° C to 90 ° C and different values of relative humidity) for a certain number of cycles or until the motor’s end of life, "says Eng. Melato. " Then, we use a well-defined duty cycle, according to the specifications of customers". During the motors test duration, each single parameter is constantly monitored and recorded (Current consumption, speed, torque and temperature).
When the motor does not meet the qualifications or does meet a default (eg an overheating, a premature wear of the brushes or the collapse of some component), it is removed for an analysis of the trouble reasons and for applying the needed improvements. After modification, the test is fully repeated for a second time, which leads to get the requested motor quality.
The unique goal is for the motor to meet all customer’s specifications and once it has entered into production to get zero waste.
The same procedure is also used once a year for products tests, in order to check that nothing has changed over the time.
Robust and reliable EMP Brakes – User’s friendly closed loop controllers
To simulate on the test benches the variable load that the motor is supposed to meet during his life, Unus chose a complete solution based on MEROBEL components, with the help of the company’s local subsidiary ANDANTEX SpA.
The chosen components were EMP brakes (type FAT120), torque sensor (type TRS50), and a closed loop controller (type DGT300).
"ANDANTEX advised us about the MEROBEL brakes to be used in this application as well as about the control unit and the various parameters to be set according to our specifications, "says Eng. Melato, "A true partnership was established with ANDANTEX about the supply of the brakes all along the application development. In particular, sharing expertise with our customized software designers, was crucial to get the final test systems fully matching our needs. "
The wide range of solutions offered by MEROBEL includes high-tech actuators such as EMP brakes and clutches, digital controllers, sensors and transducers. The specific know-how acquired by the company allows to offer optimal solutions for almost any kind of variable torque application system, according to its specific requirements.
MEROBEL EMP (ElectroMagnetic Particles) Brakes and Clutches range are made of two concentric rotors, the outside and the inside ones, separated by a gap where are located the magnetic particles.
Variation of the magnetic field in the gap (created by a variable DC current coil fed) leads to a variable “fluidity” of the magnetic particle, and leads to a smooth and variable mechanical coupling between the two rotors (variable torque).
This specific technology guarantees a stable torque, reproducible and independent of the speed of rotation, as well as easily adjustable with a low DC current level.
Among the main features of MEROBEL EMP brakes and clutches, are the proportionality between to the applied current and the provided torque, the independence between torque and speed, the bidirectional operation, very low wear and noiseless operation.
In addition, MEROBEL EMP brakes and clutches are offering low maintenance, fast response time (10 to 50 ms), low electric power consumption, linear response, very easy remote control features, and easy integration in any type of test systems.
"We have been very pleased with the MEROBEL products and the support from ANDANTEX" concluded Eng. Melato. "We had first the MEROBEL Brakes installed at the production test benches. And even if the requests were quite higher, we have now extended the use of these brakes to the laboratory test benches with great success”.