www.magazine-industry-usa.com
20
'09
Written on Modified on
OBLED-SACSUM, a SOCOM METALLURGY company, has reconditioned its POREBA boring and drilling machine using a DualDRIVE rack and pinion-drive solution from Redex Andantex
This subcontractor of high, added value complex components now has a high capacity, precision machine capable of up to 100t, with dimensions of 10m x 6m and a precision of +/- 2/100mm on positioning.
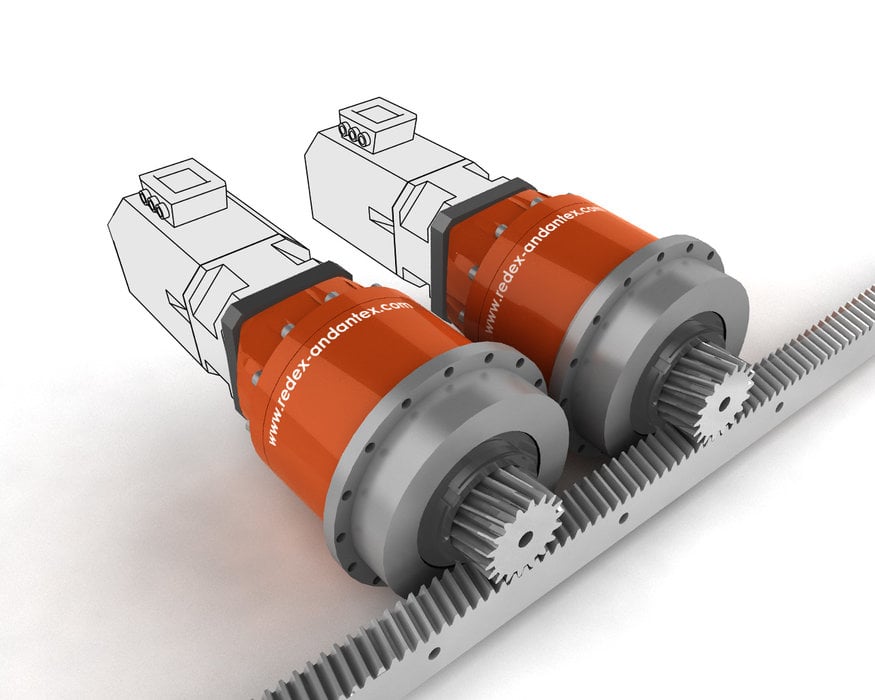
OBLED-SACSUM has a reputation in the international market as a producer of high added-value complex products. To satisfy this industrial strategy, the SOCOM METALLURGY group decided to refurbish its large capacity boring and drilling machine to make it, with a small investment, a dynamic machine-tool of the most precise on the market. High speed is a fundamental characteristic of this type of large capacity machine since it can work continuously on the same product for three weeks. It contributes directly to the profitability of the production equipment.
It should be noted that the cost of this refurbished model is 6 or 7 times less than that of an equivalent new machine.
OBLED-SACSUM, having first invested in the latest generation of numerical control, then dedicated its research efforts into precision and productivity benefits.
In this area it is clearly mechanical drives that have largely contributed to the machine’s improved performance. The critical axis is the 10,000mm stroke X axis, which is why the company decided to install a rack and pinion DualDRIVE system, from Redex Andantex.
“The specifications were essential for circular profiles” (circular interpolation on 2 synchronised axis). “Before, this was impossible for us, as the contours had to be carved,” explains M Basile, head of maintenance. “At present we are attaining tolerances of +/- 2/100mm.”
To guarantee this simultaneous rigidity, high level of precision and elevated dynamic capacity, OBLED-SACSUM chose DualDRIVE from REDEX-ANDANTEX.
“We were satisfied with our first experience of REDEX ANDANTEX, which concerned the modification of the Z axis on a large engine lathe with 8m stroke. On this machine we used a DualDRIVE rack and pinion-drive system with mechanical preload. The technical expertise of REDEX ADANTEX allowed us to advance with confidence towards the optimal solution,” adds M. Basile.
DualDRIVE is perfectly suited to the need for improved precision, due to its two fundamental characteristics:
- Very high stiffness and rigidity, beyond normal standards that allows assured, continuous servo-control up to the load limit of 100t
- Zero backlash, eliminated by using two pinions - one to drive the axis and one to preload.
In such a system, two parallel mounted servo planetary reducers are electrically coupled. The electrical preload uses a servomotor to drive each reducer, in order to simultaneously apply a frictional torque to the two pinions (to eliminate backlash) and a resulting torque for the overall drive of the system.
The high rigidity of the DualDRIVE is derived from its design: the output bearings, which are reinforced by two tapered roller bearings, preloaded and generously oversized and the output shaft pinion, which is machined directly on the output shaft. The bearing itself is designed to support the pinion as close as possible to the applied force. These features mean the DualDRIVE offers exceptional rigidity for all axes, often allowing twice the loads and speeds existing systems. The DualDRIVE design offers, in particular, a considerable reduction in radial deflection, which is the cause of 60% of overall distortion.
In the case of OBLED-SACSUM, the position is controlled in a closed loop by a linear encoder positioned on the X axis.
FURTHER INFORMATION
With around 100 employees and a turnover of €14m, OBLED-SACSUM produces all types of heavy industrial equipment (up to 100 tons) – from design through to testing in its workshops. The company also undertakes subcontract work in bending, heat treatment, shotblasting and painting applications and specialises in producing complete large dimension assemblies for the steel, offshore, specialist machines and equipment, nuclear, works of art and tunneling markets.
SOCOM METALLURGY (www.socom-metallurgy.fr) is a specialist group comprising six companies in France and one in Belgium (with 400 employees and a turnover of €55m). The OBLED SACSUM business operates under the direction of M. Begin, managing director, along with senior executives Mr Vercruysse (president) and Mr Agogue (managing director of the group).
Despite the current generally pessimistic manufacturing outlook, the group maintains its wish to invest and proceed with established technology, continuing with new production techniques offered by the market.
Picture: REDEX ANDANTEX drive systems with electrical preload
It should be noted that the cost of this refurbished model is 6 or 7 times less than that of an equivalent new machine.
OBLED-SACSUM, having first invested in the latest generation of numerical control, then dedicated its research efforts into precision and productivity benefits.
In this area it is clearly mechanical drives that have largely contributed to the machine’s improved performance. The critical axis is the 10,000mm stroke X axis, which is why the company decided to install a rack and pinion DualDRIVE system, from Redex Andantex.
“The specifications were essential for circular profiles” (circular interpolation on 2 synchronised axis). “Before, this was impossible for us, as the contours had to be carved,” explains M Basile, head of maintenance. “At present we are attaining tolerances of +/- 2/100mm.”
To guarantee this simultaneous rigidity, high level of precision and elevated dynamic capacity, OBLED-SACSUM chose DualDRIVE from REDEX-ANDANTEX.
“We were satisfied with our first experience of REDEX ANDANTEX, which concerned the modification of the Z axis on a large engine lathe with 8m stroke. On this machine we used a DualDRIVE rack and pinion-drive system with mechanical preload. The technical expertise of REDEX ADANTEX allowed us to advance with confidence towards the optimal solution,” adds M. Basile.
DualDRIVE is perfectly suited to the need for improved precision, due to its two fundamental characteristics:
- Very high stiffness and rigidity, beyond normal standards that allows assured, continuous servo-control up to the load limit of 100t
- Zero backlash, eliminated by using two pinions - one to drive the axis and one to preload.
In such a system, two parallel mounted servo planetary reducers are electrically coupled. The electrical preload uses a servomotor to drive each reducer, in order to simultaneously apply a frictional torque to the two pinions (to eliminate backlash) and a resulting torque for the overall drive of the system.
The high rigidity of the DualDRIVE is derived from its design: the output bearings, which are reinforced by two tapered roller bearings, preloaded and generously oversized and the output shaft pinion, which is machined directly on the output shaft. The bearing itself is designed to support the pinion as close as possible to the applied force. These features mean the DualDRIVE offers exceptional rigidity for all axes, often allowing twice the loads and speeds existing systems. The DualDRIVE design offers, in particular, a considerable reduction in radial deflection, which is the cause of 60% of overall distortion.
In the case of OBLED-SACSUM, the position is controlled in a closed loop by a linear encoder positioned on the X axis.
FURTHER INFORMATION
With around 100 employees and a turnover of €14m, OBLED-SACSUM produces all types of heavy industrial equipment (up to 100 tons) – from design through to testing in its workshops. The company also undertakes subcontract work in bending, heat treatment, shotblasting and painting applications and specialises in producing complete large dimension assemblies for the steel, offshore, specialist machines and equipment, nuclear, works of art and tunneling markets.
SOCOM METALLURGY (www.socom-metallurgy.fr) is a specialist group comprising six companies in France and one in Belgium (with 400 employees and a turnover of €55m). The OBLED SACSUM business operates under the direction of M. Begin, managing director, along with senior executives Mr Vercruysse (president) and Mr Agogue (managing director of the group).
Despite the current generally pessimistic manufacturing outlook, the group maintains its wish to invest and proceed with established technology, continuing with new production techniques offered by the market.
Picture: REDEX ANDANTEX drive systems with electrical preload