www.magazine-industry-usa.com
07
'08
Written on Modified on
High Tech machines are not an option
With the new GGTronic, Italian OEM GIANA decided to position itself on the higher level of machine-tools technology. “It is the only way to survive” explains Giulio Maria Giana, the company manager and technical director. As this milling & turning equipment in one set solution for big mechanical parts, very high rigidity becomes obviously a crucial design feature. Positioning has also to be very precise, reaching values as low as ±0.01mm, with a repeated accuracy of ±0.005 mm. To achieve these performances, GIUSEPPE GIANA went one step ahead by implemented REDEX-ANDANTEX’s TwinDRIVE on the machine, the original rack and pinion drive solution.
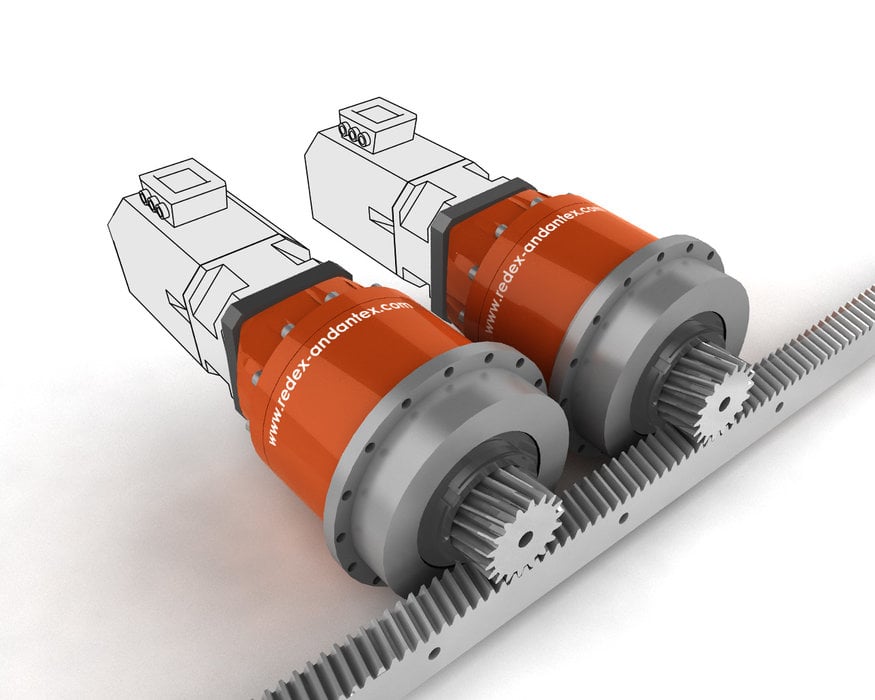
“The GGTronic outstanding performances enable us to face the pressure of the costs and the evolving needs of our customers. Formerly, our customers were looking first for power and second for high speeds. Nowadays, materials are tougher and tougher and precision requirements are becoming higher and higher”, explains Giulio Maria Giana.
The new line of GGTronic turning and milling centers can machine cylinders and complex components up to 4,000 mm in diameter and 25,000 mm in length. They are also designed to be used in a complete unmanned environment. These high powered machines are particularly suited to heavy-duty machining in the precision mechanics sector, to the machining of ship masts, wind turbine masts, turbine shafts, oil pipeline valves, crankshafts and rolls, to the machining of large winch drums, etc.
Machining process for this kind of part can last for hours and may need several types of machining before to be achieved. They have very tight tolerances despite huge weight and dimension.
On the other hand, and to make the machining process as fast as possible, traverse speeds of 20,000 mm/min can be reached, as well as accelerations up to 4 m.s-2.
The machine structure, built entirely of cast iron, is even strong enough to hold anti-vibration boring bars suitable for internal boring to a depth of over 5,000 mm.
Among all the design key points taken in account at the beginning of the project, and including for instance machine's ergonomic features (ease of clamping, tools visibility throughout the various stages of machining, access to different measurements once the part has been finished), both machining precision and machine frame’s rigidity were of course absolutely crucial.
As GIUSEPPE GIANA company’s idea with the GGTronic was that to keep its position one step ahead to the competition, the global machine’s productivity needed to be dramatically increased by eliminating most of the usual needs for regrinding the parts after machining.
That target easily explains the very high level of requests for final precision of the machine, and then the very high level of global stiffness which is mandatory to reach this level of precision under dynamic conditions.
Rigidity and precision are achieved through a unique technological concept
The main technical issue in terms of rigidity was the Z axis which features the longest strokes (up to 25.000 mm).
To ensure getting the best performances from the chosen linear drive technology, GIUSEPPE GIANA decided to implement a TwinDRIVE Rack & Pinions system produced by REDEX ANDANTEX. This turnkey system offers unique innovations which enables outstanding performances.
And the final results were clearly reaching the designer’s expectations with positioning precision and repeatability as low as ± 0.01 and ± 0.005 mm, together with an exceptional global stiffness.
TwinDRIVE Rack & Pinion drive systems are made up of 2 parallel mounted planetary servo reducers that are coupled electrically. This preload system eliminates the backlash and contributes to offer high precision.
Extreme rigidity is provided in all directions by an integrated output pinion shaft supported by reinforced output bearings. This unique REDEX ANDANTEX concept provides torsional stiffness characteristics that are among the best on the market, but it mostly offers exceptional rigidity along the other axes; this often enables use of up to twice the acceleration rates or weight capacities of other solutions.
This exclusive design combines strongly reinforced output bearings with pinions integrated to the output shaft (chill cast, case hardened and ground, and the same diameter as the shaft). The pitch diameter is optimized to ensure the best ratio between the torque transmitted and rigidity as seen from the rack point of view. The bearing arrangement himself consists in two tapered roller bearings, preloaded and generously oversized. This bearings arrangement is designed to support the pinion as close as possible to the applied force, with only the thickness of the locknut separating the pinion from the output bearing. This particular design provides a considerable reduction in radial deflection, which is the cause of 60% of overall deformation but which is usually not dealt with satisfactorily by other systems.
In addition, as for the longitudinal axis, the X and Y axes also slide on preloaded roller guide shoes. With a B-axis machine, parts can be machined both on 5 sides, in a single setup, or by using all 5 axes to machine any complex profile. If the machine also has a B axis, the piece can be worked on five sides after being positioned only once, and the five axes may be interpolated to make any kind of complex profile.
Making the mechanical gearing a modular system
“This is not the only advantage we get from REDEX-ANDANTEX”, add Giulio Maria Giana. “Before, each time we had to answer to a customer specific request, we had to rebuild the complete mechanical drive system. It was a lot of work to change. Adjusting power and speed meant changing several components including the reducer. Now, we just have to indicate the power and the speed and REDEX-ANDANTEX is preparing the right Rack & Pinions system. Modifying everything, including the Speed / Load Ratio is very simple.”
A successful launching
“With this high precision and rigidity machine, we have served traditional markets such as the USA, Denmark, the Netherlands, etc. but also emerging markets such as China and India. There are no limits on the foreign markets we may serve: we go wherever our technology is needed.
The principal sectors we serve are still the same: energy, oil and the aerospace industries, but we will not neglect any other sector that needs machine tools of the type we produce, that is, large scale lathes, perforators and superfinishing machines. All these machines have a teleservice feature, both for PLCs and NC, guaranteeing the high quality of Giuseppe Giana Spa’s technical assistance service”.
Amongst the last orders, we can quote CELSA in Poland for wind propellers manufacturing or Nordmark Maskinfabrik in Denmark. Parts of more than 80T can be machined.
For this company, once the GGTronic 3000 installed, a quick calibration and adjustment on the Z-axis scale has been made. Then a VDI3441 test has been carried on all axes.
Results from these measuring on the Z-axis can be seen below. A precision close to 0.01 mm has been achieved in a short period of time. Performances on the X axis are close to the micron, for the milling, turning and boring processes.
Giuseppe Giana Spa is located in Magnago, in the province of Milan, in 10,000 square meters of buildings. The company’s large pool of advanced machine tools is destined for work on contract and construction of a number of components of its own machines.
Giuseppe Giana Spa makes grinders, boring machines, milling machines and milling and planning machines, including the Europe’s biggest grinder for flat surfaces. Giulio Maria Giana explains: “we will be continuing to focus more and more on international markets with highly specialized multitasking lathes”.
The new line of GGTronic turning and milling centers can machine cylinders and complex components up to 4,000 mm in diameter and 25,000 mm in length. They are also designed to be used in a complete unmanned environment. These high powered machines are particularly suited to heavy-duty machining in the precision mechanics sector, to the machining of ship masts, wind turbine masts, turbine shafts, oil pipeline valves, crankshafts and rolls, to the machining of large winch drums, etc.
Machining process for this kind of part can last for hours and may need several types of machining before to be achieved. They have very tight tolerances despite huge weight and dimension.
On the other hand, and to make the machining process as fast as possible, traverse speeds of 20,000 mm/min can be reached, as well as accelerations up to 4 m.s-2.
The machine structure, built entirely of cast iron, is even strong enough to hold anti-vibration boring bars suitable for internal boring to a depth of over 5,000 mm.
Among all the design key points taken in account at the beginning of the project, and including for instance machine's ergonomic features (ease of clamping, tools visibility throughout the various stages of machining, access to different measurements once the part has been finished), both machining precision and machine frame’s rigidity were of course absolutely crucial.
As GIUSEPPE GIANA company’s idea with the GGTronic was that to keep its position one step ahead to the competition, the global machine’s productivity needed to be dramatically increased by eliminating most of the usual needs for regrinding the parts after machining.
That target easily explains the very high level of requests for final precision of the machine, and then the very high level of global stiffness which is mandatory to reach this level of precision under dynamic conditions.
Rigidity and precision are achieved through a unique technological concept
The main technical issue in terms of rigidity was the Z axis which features the longest strokes (up to 25.000 mm).
To ensure getting the best performances from the chosen linear drive technology, GIUSEPPE GIANA decided to implement a TwinDRIVE Rack & Pinions system produced by REDEX ANDANTEX. This turnkey system offers unique innovations which enables outstanding performances.
And the final results were clearly reaching the designer’s expectations with positioning precision and repeatability as low as ± 0.01 and ± 0.005 mm, together with an exceptional global stiffness.
TwinDRIVE Rack & Pinion drive systems are made up of 2 parallel mounted planetary servo reducers that are coupled electrically. This preload system eliminates the backlash and contributes to offer high precision.
Extreme rigidity is provided in all directions by an integrated output pinion shaft supported by reinforced output bearings. This unique REDEX ANDANTEX concept provides torsional stiffness characteristics that are among the best on the market, but it mostly offers exceptional rigidity along the other axes; this often enables use of up to twice the acceleration rates or weight capacities of other solutions.
This exclusive design combines strongly reinforced output bearings with pinions integrated to the output shaft (chill cast, case hardened and ground, and the same diameter as the shaft). The pitch diameter is optimized to ensure the best ratio between the torque transmitted and rigidity as seen from the rack point of view. The bearing arrangement himself consists in two tapered roller bearings, preloaded and generously oversized. This bearings arrangement is designed to support the pinion as close as possible to the applied force, with only the thickness of the locknut separating the pinion from the output bearing. This particular design provides a considerable reduction in radial deflection, which is the cause of 60% of overall deformation but which is usually not dealt with satisfactorily by other systems.
In addition, as for the longitudinal axis, the X and Y axes also slide on preloaded roller guide shoes. With a B-axis machine, parts can be machined both on 5 sides, in a single setup, or by using all 5 axes to machine any complex profile. If the machine also has a B axis, the piece can be worked on five sides after being positioned only once, and the five axes may be interpolated to make any kind of complex profile.
Making the mechanical gearing a modular system
“This is not the only advantage we get from REDEX-ANDANTEX”, add Giulio Maria Giana. “Before, each time we had to answer to a customer specific request, we had to rebuild the complete mechanical drive system. It was a lot of work to change. Adjusting power and speed meant changing several components including the reducer. Now, we just have to indicate the power and the speed and REDEX-ANDANTEX is preparing the right Rack & Pinions system. Modifying everything, including the Speed / Load Ratio is very simple.”
A successful launching
“With this high precision and rigidity machine, we have served traditional markets such as the USA, Denmark, the Netherlands, etc. but also emerging markets such as China and India. There are no limits on the foreign markets we may serve: we go wherever our technology is needed.
The principal sectors we serve are still the same: energy, oil and the aerospace industries, but we will not neglect any other sector that needs machine tools of the type we produce, that is, large scale lathes, perforators and superfinishing machines. All these machines have a teleservice feature, both for PLCs and NC, guaranteeing the high quality of Giuseppe Giana Spa’s technical assistance service”.
Amongst the last orders, we can quote CELSA in Poland for wind propellers manufacturing or Nordmark Maskinfabrik in Denmark. Parts of more than 80T can be machined.
For this company, once the GGTronic 3000 installed, a quick calibration and adjustment on the Z-axis scale has been made. Then a VDI3441 test has been carried on all axes.
Results from these measuring on the Z-axis can be seen below. A precision close to 0.01 mm has been achieved in a short period of time. Performances on the X axis are close to the micron, for the milling, turning and boring processes.
Giuseppe Giana Spa is located in Magnago, in the province of Milan, in 10,000 square meters of buildings. The company’s large pool of advanced machine tools is destined for work on contract and construction of a number of components of its own machines.
Giuseppe Giana Spa makes grinders, boring machines, milling machines and milling and planning machines, including the Europe’s biggest grinder for flat surfaces. Giulio Maria Giana explains: “we will be continuing to focus more and more on international markets with highly specialized multitasking lathes”.