www.magazine-industry-usa.com
19
'24
Written on Modified on
ADVANCEMENTS IN INDUSTRIAL DRIVE SYSTEMS
As the industry shifts toward electrification, industrial drives are proving indispensable in reducing reliance on fully hydraulic systems – K.A. Gerardino.
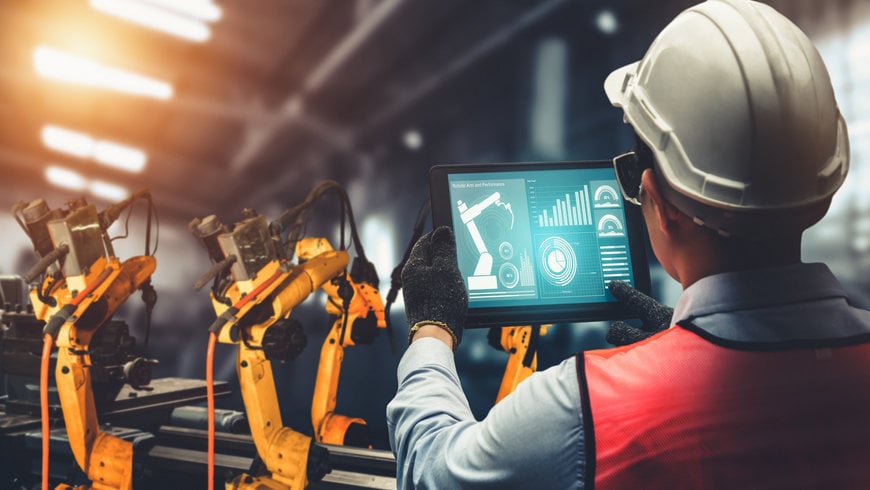
Industrial drive systems are the beating heart of modern manufacturing and automation. These essential systems, which control the speed, torque, and direction of machinery, play a crucial role in industries ranging from automotive and aerospace to food and beverage and heavy machinery. In recent years, the market for industrial drive systems has evolved rapidly, spurred by the growing demand for energy efficiency, precision, and seamless automation.
On the factory floor, industrial drive systems are key players in the next generation of automation. These systems, known as electrical drives, control the motion of electrical machines with remarkable precision. At the core of a typical drive system is an electric motor, paired with an advanced control system that manages the motor shaft's rotation. Depending on the application—whether it’s turning shafts, driving pumps, or powering fans—different types of motors are employed to meet specific requirements.
As the industry shifts toward electrification, industrial drives are proving indispensable in reducing reliance on fully hydraulic systems. By embracing various types of industrial drives, OEMs (Original Equipment Manufacturers) are at the forefront of this transition, pushing the boundaries of what's possible in modern manufacturing.
Market Overview
The global industrial drive systems market is experiencing steady growth, with a compound annual growth rate (CAGR) projected to be around 5-7% from 2023 to 2030. This growth is primarily fueled by the rising adoption of automation in manufacturing, the need for energy-efficient solutions, and the expansion of industries in emerging economies.
Key Regions
The market is witnessing varied growth patterns across different regions, each shaped by specific economic and industrial factors. In North America, the market is being propelled by the adoption of advanced manufacturing practices and a robust demand for automation. Companies in this region are increasingly investing in innovative technologies to enhance production efficiency, reduce operational costs, and meet the growing demand for high-quality products.
Europe, on the other hand, is focused on driving the market through initiatives aimed at energy efficiency and sustainability. Governments and industries in this region are emphasizing the reduction of carbon footprints and energy consumption, which in turn fuels the demand for energy-efficient industrial drive systems. This focus aligns with Europe's broader goals of achieving sustainable industrial growth and addressing environmental concerns.
In the Asia-Pacific region, rapid industrialization is the key driver of market expansion. China and India, as the region's largest economies, are at the forefront of this growth. The surge in manufacturing activities, infrastructure development, and technological advancements in these countries is creating a significant demand for industrial drive systems. This growth is further supported by favorable government policies, foreign investments, and a growing emphasis on modernizing industrial processes.
Latin America and Africa are emerging as important markets in the global industrial drive systems sector. These regions are experiencing increasing industrial activities, driven by economic development and investments in infrastructure and manufacturing. As industries in Latin America and Africa continue to grow and modernize, the demand for reliable and efficient industrial drive systems is expected to rise steadily, contributing to the overall growth of the market.
Together, these regions paint a comprehensive picture of a global market that is both diverse and dynamic, with each area contributing to the advancement and proliferation of industrial drive systems in its unique way.
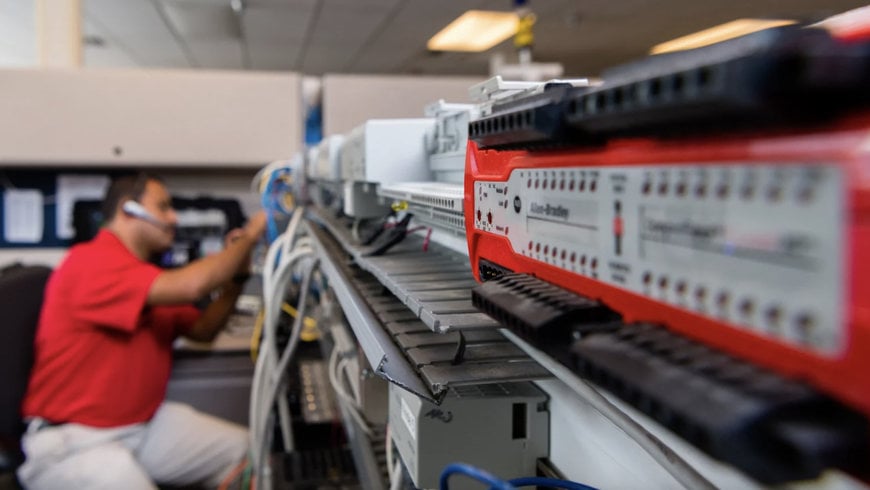
Image: Rockwell Automation
Types of Industrial Drive Systems
Industrial drive systems are essential components in modern manufacturing and automation processes, providing the necessary control and power to various types of machinery. Among the most widely used are AC drives, DC drives, servo drives, and stepper drives, each offering distinct advantages tailored to specific industrial applications.
AC drives, or variable frequency drives (VFDs), are the most prevalent type of industrial drive systems, primarily due to their efficiency and versatility. These drives control the speed of electric motors by varying the frequency and voltage supplied to the motor, allowing for precise control over motor performance. The widespread adoption of AC drives across various industries—from manufacturing to HVAC systems—stems from their ability to enhance energy efficiency, reduce operational costs, and improve process control. Their dominance in the market is also attributed to their robustness and ease of integration into existing systems, making them a preferred choice for applications ranging from conveyor belts to large-scale industrial pumps and fans.
While AC drives have become the standard in many industries, DC drives still hold a significant place in applications that demand high torque and precise speed control. DC drives regulate the speed and torque of direct current motors, making them ideal for processes where consistent and accurate control is critical. Although less common than their AC counterparts, DC drives are particularly valued in applications such as hoists, cranes, and other heavy machinery that require substantial starting torque and fine-tuned speed adjustments. Their simplicity in control and maintenance continues to make DC drives a reliable option in specific industrial settings.
Servo drives are specialized systems designed for applications where precise control of position, speed, and torque is paramount. These drives are integral to the operation of sophisticated machinery, such as robotics, CNC (Computer Numerical Control) machines, and automated assembly lines. Servo drives work in conjunction with servo motors, using feedback mechanisms to ensure exact positioning and movement, which is essential for tasks requiring high accuracy and repeatability. The advanced control capabilities of servo drives make them indispensable in industries like electronics manufacturing, automotive production, and aerospace engineering, where precision is non-negotiable.
Stepper drives are another category of industrial drive systems known for their ability to control the precise positioning of motors. These drives operate by sending pulses to the motor, with each pulse corresponding to a fixed movement or "step." This makes stepper drives ideal for applications that demand exact movement control, such as in 3D printers, CNC machines, and other automated equipment where accuracy is crucial. Unlike servo drives, stepper drives do not require feedback for positioning, making them simpler and more cost-effective for certain types of operations. However, they are best suited for low-to-medium torque applications, where precision in positioning takes precedence over speed.
Each type of industrial drive system plays a vital role in modern automation and manufacturing, with specific applications determining the most suitable option. AC drives dominate the landscape due to their versatility and efficiency, while DC drives continue to be favored for high-torque, precision-controlled applications. Servo drives excel in environments where exact positioning and control are critical, and stepper drives offer a cost-effective solution for precision positioning tasks. Together, these drive systems form the backbone of industrial operations, enabling the automation and efficiency that modern industries require to stay competitive.
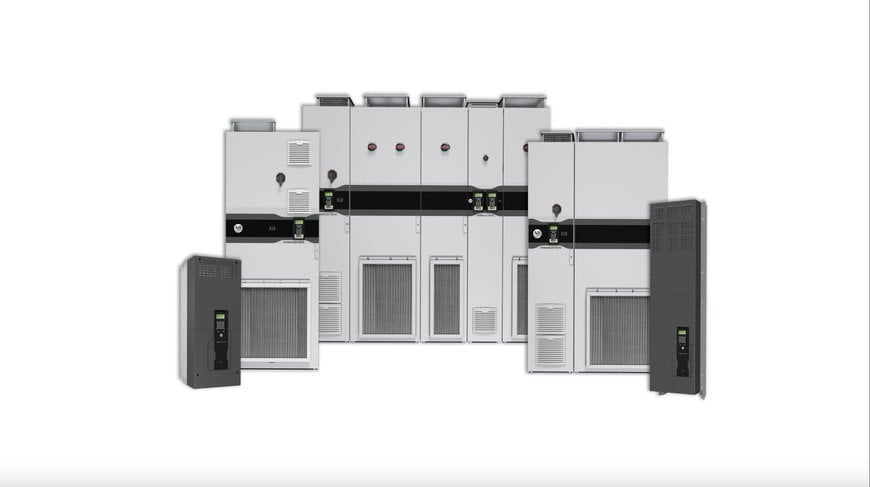
PowerFlex 755T VFD Image: Rockwell Automation
Advancements in Industrial Drive Systems
The landscape of industrial drive systems is evolving rapidly, driven by technological innovations and the growing demands of modern industries. As manufacturers strive to enhance efficiency, precision, and reliability, several key advancements are shaping the future of industrial drive systems. These developments not only address current industry challenges but also pave the way for more sophisticated and adaptable solutions.
Energy Efficiency
One of the most significant advancements in industrial drive systems is the focus on energy efficiency. As industries become increasingly aware of their environmental impact and energy costs, the demand for energy-efficient drive systems has surged.
Manufacturers are developing drives that minimize energy consumption while maintaining high performance. A notable innovation in this area is the use of regenerative drives. These systems have the capability to capture and convert the energy generated during braking processes and feed it back into the grid. This not only reduces the overall energy consumption of industrial operations but also contributes to a more sustainable and cost-effective energy management strategy. Furthermore, energy-efficient drives are being designed with advanced power electronics and control technologies that optimize energy usage without compromising the performance of the motors they control.
Integration with the Industrial Internet of Things (IIoT)
The integration of Industrial Internet of Things (IIoT) technologies into industrial drive systems represents a transformative shift in how these systems are monitored, managed, and optimized. IIoT-enabled drives, often referred to as "smart drives," are equipped with sensors and communication modules that allow for real-time data collection and analysis. This capability enables predictive maintenance, where potential issues can be identified and addressed before they lead to costly downtime. Additionally, smart drives provide insights into performance metrics, allowing operators to fine-tune operations for maximum efficiency. The integration of IIoT also facilitates remote monitoring and control, enabling industrial systems to be managed from virtually anywhere, further enhancing operational flexibility and responsiveness.
Enhanced Precision and Control
The demand for higher precision and control in industrial processes has driven significant advancements in the design of industrial drive systems. With the development of sophisticated digital signal processing (DSP) technologies and advanced control algorithms, modern drives offer unparalleled levels of accuracy, speed, and reliability. These improvements are crucial in industries such as automotive, aerospace, and electronics manufacturing, where even the slightest deviation can lead to significant quality issues. Enhanced control capabilities also allow for more complex and dynamic operations, supporting the growing trend towards automation and the use of robotics in manufacturing. The ability to achieve higher precision and faster response times not only improves product quality but also increases overall production efficiency.
Customization and Flexibility
As industries diversify and the need for specialized applications grows, the demand for customizable and flexible drive systems has become more pronounced. Manufacturers are responding by developing modular drive systems that can be easily configured and adapted to meet specific operational requirements. These modular systems offer the advantage of scalability, allowing users to upgrade or modify their drive systems as needed without requiring a complete overhaul. This flexibility is particularly valuable in industries where production needs can change rapidly, such as in consumer electronics or custom manufacturing. Customizable drive systems also support the integration of additional features, such as specialized control interfaces or application-specific software, further enhancing their utility and adaptability in diverse industrial environments.
Miniaturization and Compact Designs
Space constraints are a growing concern in many industrial settings, particularly in urban environments or highly automated facilities where floor space is at a premium. In response, there has been a marked trend towards the development of smaller, more compact drive systems that do not sacrifice performance for size. Advances in materials science, thermal management, and microelectronics have enabled the creation of miniaturized drives that are both powerful and efficient. These compact systems are ideal for applications where space is limited but high-performance is still required, such as in robotics, medical devices, and portable industrial equipment. The ability to incorporate powerful drive capabilities into smaller form factors also supports the broader trend towards automation and the use of intelligent machinery in industries ranging from logistics to precision manufacturing.
The advancements in industrial drive systems reflect the broader trends in technology and industry towards greater efficiency, precision, and adaptability. As energy efficiency becomes a paramount concern, the development of regenerative and power-optimized drives is helping industries reduce their environmental impact and operational costs. The integration of IIoT technologies is revolutionizing how drive systems are managed, offering real-time insights and predictive capabilities that enhance reliability and performance. Enhanced precision and control are enabling more complex and high-quality manufacturing processes, while the trend towards customization and modularity is providing industries with the flexibility to adapt to changing needs. Finally, the move towards miniaturization is allowing for the deployment of powerful drive systems in increasingly compact spaces, supporting the ongoing evolution of industrial automation and efficiency. Together, these advancements are driving the future of industrial operations, enabling more intelligent, efficient, and versatile manufacturing environments.
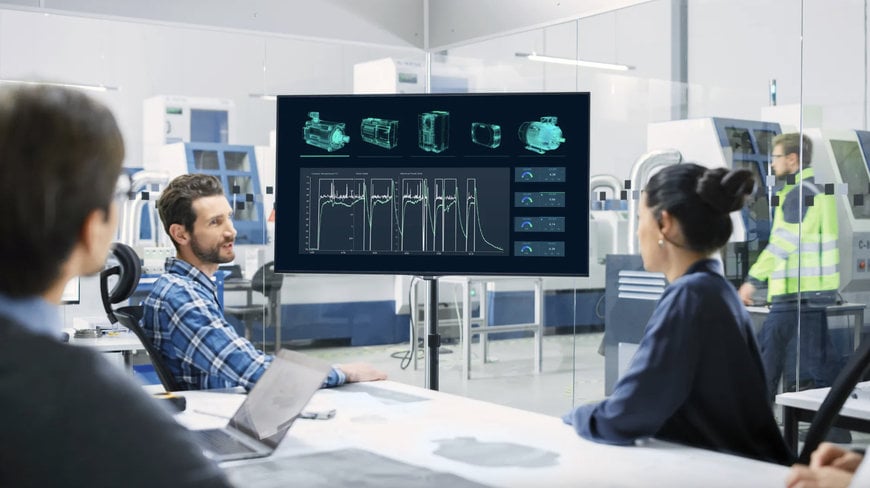
Image: Siemens
Key Market Drivers in Industrial Drive Systems
The industrial drive systems market is experiencing robust growth, driven by several key factors that are reshaping the landscape of modern manufacturing and automation. Among these drivers, the push towards automation and Industry 4.0, the implementation of stricter energy regulations, and continuous technological advancements are playing pivotal roles. These factors are not only influencing market dynamics but are also prompting significant investments and innovations by leading companies in the industry.
Automation and Industry 4.0
The global shift towards automation and smart manufacturing, often referred to as Industry 4.0, is one of the most significant drivers of the industrial drive systems market. Industry 4.0 encompasses the integration of digital technologies, such as artificial intelligence (AI), machine learning (ML), big data analytics, and the Internet of Things (IoT), into manufacturing processes. This technological revolution is transforming traditional manufacturing environments into highly automated, interconnected systems where real-time data is used to optimize production, reduce waste, and increase efficiency.
As industries increasingly adopt Industry 4.0 technologies, the demand for advanced drive systems that can seamlessly integrate with these smart manufacturing ecosystems is expected to rise. These drive systems need to be highly responsive, capable of real-time adjustments, and able to communicate with other components within the manufacturing process. For instance, Siemens, a global leader in automation technology, has been at the forefront of developing smart drive systems that align with Industry 4.0 principles. Their SINAMICS drive series, for example, is designed to support digitalization in manufacturing by offering enhanced connectivity, advanced diagnostics, and integration with Siemens' broader digital automation platform.
Another key player, ABB, has been focusing on providing drive systems that cater to the evolving needs of Industry 4.0. ABB’s drive solutions are increasingly equipped with IoT capabilities, allowing for predictive maintenance and real-time monitoring, which are crucial for maintaining the high levels of efficiency and reliability demanded by smart factories.
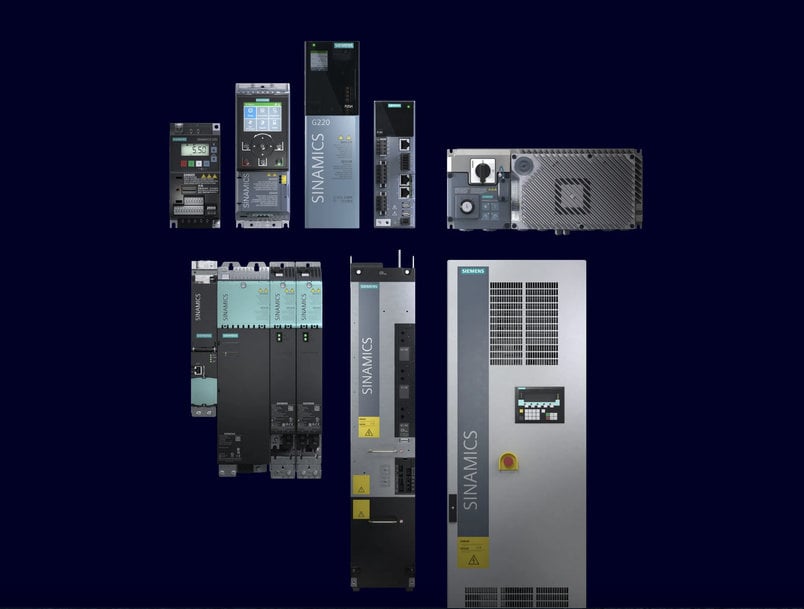
SINAMICS variable frequency drives Image: Siemens
Energy Regulations
The push towards greater energy efficiency is another critical factor driving the adoption of advanced industrial drive systems. Around the world, governments are implementing stricter energy efficiency regulations aimed at reducing industrial energy consumption and minimizing environmental impact. These regulations are compelling industries to invest in energy-efficient technologies, including advanced drive systems, which can significantly reduce energy usage in industrial applications.
For example, the European Union's Ecodesign Directive sets stringent energy efficiency requirements for electric motors and variable speed drives, which are widely used in industrial settings. This has led to a surge in demand for energy-efficient drive systems that comply with these regulations. Companies like Schneider Electric are responding to this demand by developing drive solutions that not only meet but exceed regulatory requirements. Schneider Electric’s Altivar Process drives are designed to deliver superior energy efficiency, reducing energy consumption by up to 30% compared to conventional drives, while also providing enhanced performance and reliability.
In the United States, the Department of Energy (DOE) has also established regulations aimed at improving the energy efficiency of electric motors and drives. To comply with these regulations, companies such as Rockwell Automation are producing energy-efficient drive systems that help industrial facilities reduce their carbon footprint and operational costs. Rockwell’s PowerFlex drives, for instance, are engineered to optimize energy use, providing businesses with a sustainable solution that aligns with both regulatory requirements and corporate sustainability goals.
Technological Advancements
The continuous innovation in drive technologies is a major force propelling the industrial drive systems market forward. Technological advancements are enabling the development of more sophisticated and capable drive systems that meet the increasingly complex needs of modern industries. One of the key areas of innovation is in the development of multi-level inverters, which offer higher efficiency, reduced harmonic distortion, and improved power quality compared to traditional inverters.
These advanced inverters are particularly beneficial in applications where precision and energy efficiency are critical. Mitsubishi Electric, a leader in drive technology, has been pioneering the development of multi-level inverter technology to enhance the performance and efficiency of its drive systems. Mitsubishi’s FR-A800 series drives, for example, incorporate advanced inverter technology to provide superior motor control and energy savings, making them ideal for use in energy-intensive industries such as automotive manufacturing and chemical processing.
Another significant technological advancement in the drive systems market is the use of advanced semiconductor materials, such as silicon carbide (SiC) and gallium nitride (GaN). These materials offer higher thermal conductivity, faster switching speeds, and greater efficiency compared to traditional silicon-based semiconductors. As a result, drives utilizing SiC and GaN technologies can operate at higher voltages and temperatures, making them more efficient and reliable in demanding industrial environments. Infineon Technologies, a leading semiconductor manufacturer, has been at the forefront of incorporating SiC technology into its drive systems, enabling more compact, energy-efficient, and durable solutions for industrial applications.
The industrial drive systems market is being shaped by several critical drivers, including the global push towards automation and Industry 4.0, the tightening of energy efficiency regulations, and ongoing technological advancements. These factors are not only accelerating the adoption of advanced drive systems but also prompting key industry players to innovate and adapt their offerings to meet the evolving needs of modern industries. As companies like Siemens, ABB, Schneider Electric, Rockwell Automation, Mitsubishi Electric, and Infineon Technologies continue to lead the way with cutting-edge solutions, the future of industrial drive systems looks poised for continued growth and transformation.
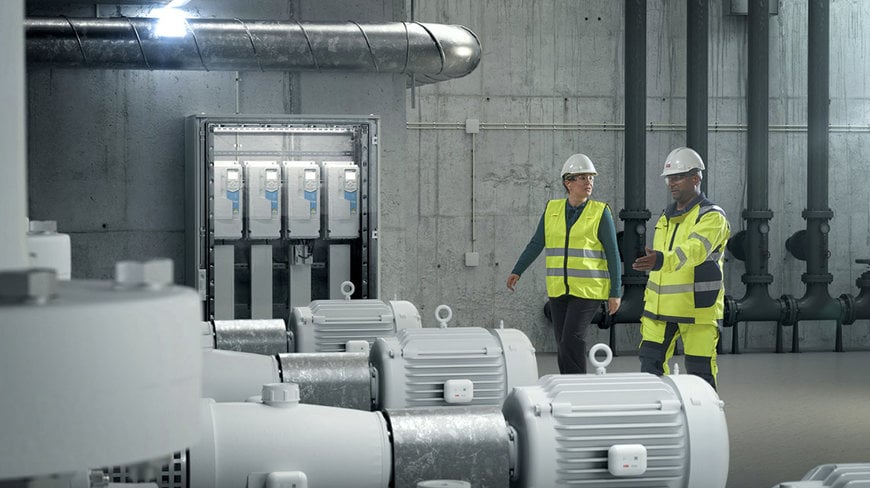
Image: ABB
Challenges in Adopting Advanced Industrial Drive Systems
While advanced industrial drive systems offer numerous benefits, their adoption comes with several challenges that industries must navigate. These challenges can be particularly daunting for small and medium-sized enterprises (SMEs) and for operations in regions with limited access to specialized expertise.
High Initial Costs
One of the most significant barriers to the widespread adoption of advanced drive systems is the high initial investment required. These systems often come with a substantial price tag due to the sophisticated technology, engineering, and components involved. For small and medium-sized enterprises, the upfront costs can be prohibitive, making it difficult to justify the investment, especially in industries with tight profit margins. Even though these systems can lead to long-term savings through improved efficiency and reduced energy costs, the initial financial outlay remains a significant hurdle for many businesses.
Complexity of Integration
Integrating advanced drive systems into existing industrial environments can be a complex and challenging process. These systems often need to be compatible with a wide range of existing machinery and processes, which can vary greatly in age, technology, and functionality. The integration process may require significant customization and reconfiguration, leading to increased downtime and disruption of operations. Moreover, this complexity often demands specialized expertise in both the technology itself and the specific industrial processes it will be applied to. For many companies, particularly those without in-house technical teams, the need to bring in external experts can add to the overall cost and complexity of adopting advanced drive systems.
Maintenance and Skill Gaps
Once advanced drive systems are implemented, maintaining and operating them presents another set of challenges. These systems often require specialized skills and knowledge, which can be difficult to find, particularly in regions where there is a shortage of skilled labor. The rapid pace of technological advancement means that maintenance teams need to be continuously trained and updated on the latest systems and software. For companies operating in areas where access to such expertise is limited, this can lead to increased reliance on external service providers, which may raise operational costs and potentially lead to delays in addressing technical issues. Additionally, the skill gap can hinder the full utilization of advanced drive systems, as operators may not be fully equipped to leverage all the capabilities these systems offer.
Conclusion
The adoption of advanced industrial drive systems, while beneficial, is not without its challenges. High initial costs, the complexity of integration, and the need for specialized maintenance skills pose significant hurdles, particularly for SMEs and companies in regions with limited access to expertise. Addressing these challenges requires careful planning, investment in training, and often, collaboration with external experts to ensure that the full potential of these advanced systems can be realized. As industries continue to evolve, overcoming these obstacles will be crucial in maximizing the benefits of advanced drive technologies.
Industrial drive systems are integral to the efficiency and productivity of modern manufacturing processes. As the market continues to evolve with technological advancements and increasing demand for energy efficiency, companies must stay ahead of the curve by adopting the latest innovations and addressing the challenges posed by cost and complexity. The future of industrial drive systems is bright, with significant growth potential in both developed and emerging markets.